如何将图上的车量产?制造过程是怎样的?涉及的范围有多广?
汽车制造确实是一个太大的话题,这个过程涉及到的问题有很多,试着答一下,不懂的地方就少说一点,请见谅。
先抛出我的理解:我认为一辆车的制造是需要大量的人力物力的,它发生在真正的“制造”之前,并一直延续到车辆出厂。
我觉得汽车制造不能仅仅将四大车间与全局割裂开。例如:四大车间是手段,但质量管理是使这个手段朝着正确的方向顺利地进行的保证,事实上质量管理确实是伴随着整个汽车制造过程的,甚至是先于正式的汽车生产的。
一辆新车从构思设计到成批生产耗资是十分巨大的,车身设计开发的费用和时间大约占到整辆汽车开发费用和时间的70%左右。
所以先来说说车身开发问题。
车身开发过程主要分为以下过程:
1)车身边界及总布置方案。
车身边界是指车身的基本技术数据及主要部件安装坐标位置的设定。整车总布置提供了汽车的长、宽、高、轴距等控制尺寸,轴荷分布范围以及散热器、动力总成、前后桥、传动轴与车轮等轮廓尺寸和位置。要注意满足相关的性能以及法规要求,并以设计理念出发,平衡各项性能。在汽车内部设计上面现在人机工程学的应用也越来越多,重视力度也越来越大。
2)基型开发
找到车身外型、总布置设计方案及空气动力学特性这三者间的最佳关系。
3)批量开发
下图是车身开发设计的示意图。
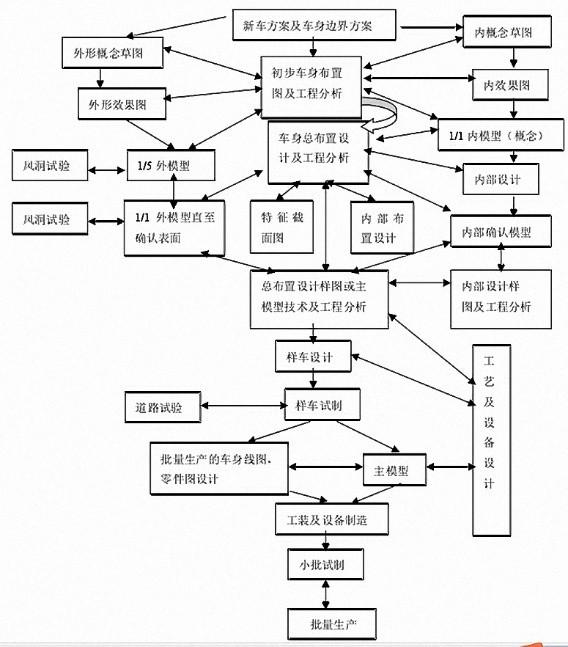
当然了基于成本、时间、风格的考虑,并不是每个部分都需要从新开发的,以SGM某年某款车型为例,下图为部分开发思路。
这也是同平台生产的特点之一。
要说四大车间问题,我觉得先要了解质量管理体系问题。
质量管理体系在在各个车企都有所不同,大方向来说有:德国的VDA6.1、美国的QS9000、法国的EAQF、意大利的ASQV、日本的精益生产。
这些都是基于ISO/TS 16949建立起来的(举例来说ISO/TS 16949:2002是有美国AIAG、德国VDA-QMC、法国CCFA/FIEV、意大利ANFIA、英国SMMT、日本JAMA、ISO/TC176联合编制的)。
具体的实施手段有很多,比如“2mm”工程、“5S管理理”、PDCA、PCA、GCA、Apk/Cpk、FMEA、JIS、TPM、PCR、GCA、DRL等等,这个话题太大就不展开了。但是需要说明的是正是建立了质量管理体系才使得产品质量得到保证、产品生产得以顺利进行。
下面再来说说四大车间。
四大车间即:冲压、车身、油漆、总装。
冲压:
冲压车间顾名思义就是制备车身的冲压件。现在由于车企综合考虑的结果(成产成本、质量要求、时间、员工成本等),大部分覆盖件都进行外包生产了,一些大型的比较重要的例如四门两盖之类的可能还是在整车厂生产。所以冲压车间相对来说是比较注重与供应商联系的车间之一。
汽车冲压件品种繁多,如汽车减震器冲压件弹簧托盘、弹簧座、弹簧托架、端盖、封盖、压缩阀盖、压缩阀套、油封座、防尘盖、叶轮、油筒、支架等都属于汽车冲压件。在汽车冲压件中,一部分经冲压后直接成为汽车零部件,另一部分经冲压后还需经过焊接、机械加工、油漆等工艺加工后才能成为汽车零部件。
一般冲压件的基本工艺流程为:
拉深——切边(冲孔)——翻边
下图为比较常见的冲压模具。
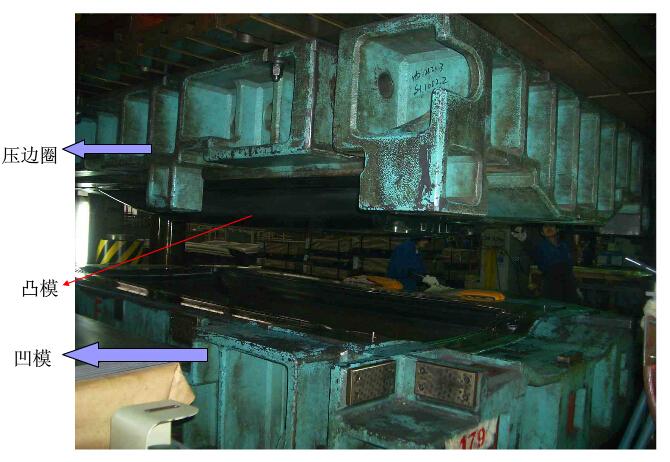
通过冲压后我们可以得到大大小小的很多冲压件。
比如这样的
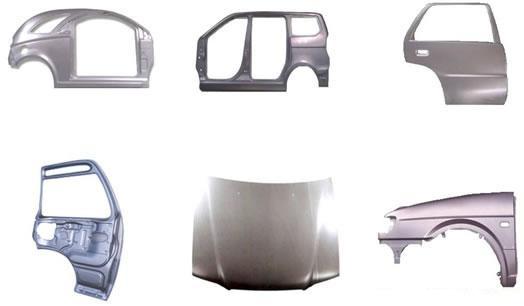
或者这样的
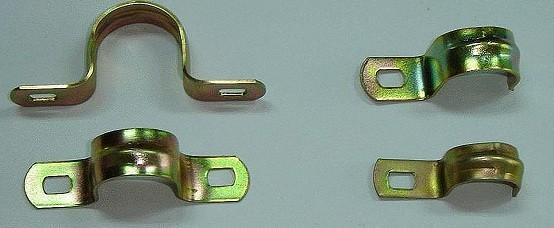
当然了,汽车上并不是只有冲压件的,铸造件也占有一定比重。一般来说缸盖、缸体、变速箱壳、曲轴、活塞、制动鼓等都是铸造件。
下图就是某款汽车空调前盖的铸造件,是采用铝合金重力铸造方式。
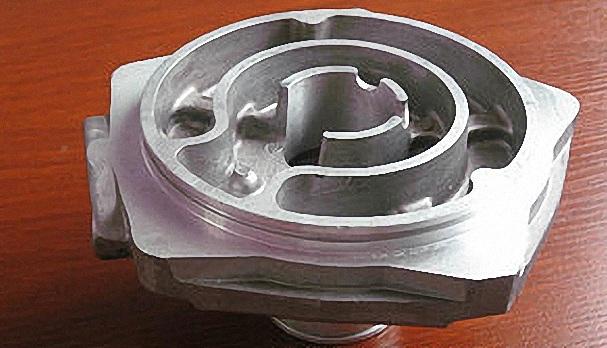
焊接:
白车身焊接即是将各种冲压件通过焊接的方式装配成合格的白车身总成。这个过程涉及到的焊接方法有很多,比如:电阻点焊、螺柱焊、铆接、激光焊/激光钎焊、CO2气体保护焊、MIG/TIG焊、Plasma焊等等。
先来了解一下一般白车身焊接的工艺流程,以某一款车型为例:
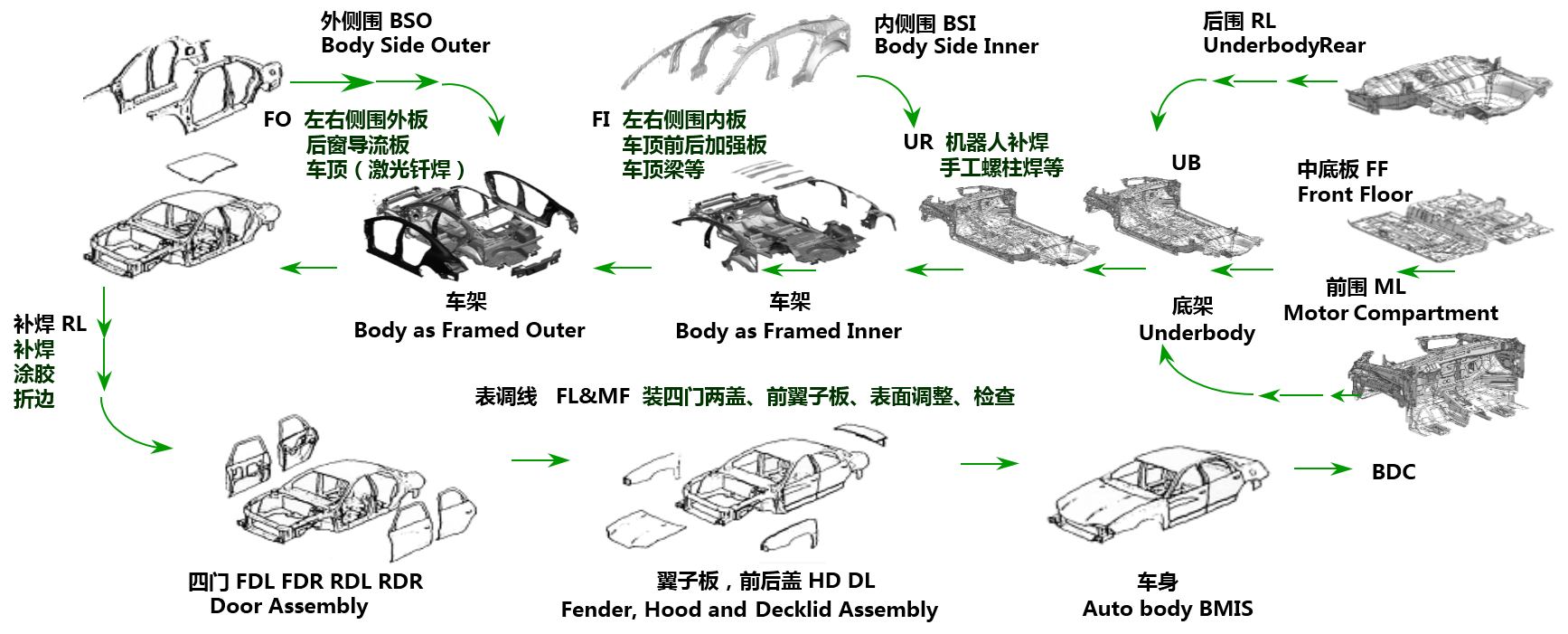
上面这个图我觉得表达比较清楚了。
需要补充的是:焊接并不是简单地将各部件焊接到一起这么简单,焊接的准确性、合理性和合法性都是需要被严格监控的。
这就引出了白车身质量监控问题了。
主要分为为五大类:
1)焊接质量监控
主要针对的是焊点的检测以及参数的控制,包括非破坏性检验和破坏性检验两大类;
2)车身功能尺寸监控
功能尺寸主要是指单件或总成的性质、大小和位置的尺寸公差,包括单个零件间的间隙、平度、面差以及和整车功能有关的尺寸。包括在线监控和线下监控;
3)扭矩质量监控
要求100%检测,通常采用扭矩扳手对紧固件打紧;
4)表面质量监控
一般针对表面有无凹陷、凸起、错位、飞溅、毛刺等缺陷,采用目检、AUDIT评审等方法;
5)涂胶质量监控
主要是针对胶量和涂胶位置两个方面进行控制。
油漆:
车身涂装是一个很复杂的工艺,在进行车身涂装的过程中,不同的阶段使用不同的涂料,不同的涂料形成不同的漆层。车的漆面在传统涂装工艺中被分为四层,共同对车身起着保护和美观的功能;对于一般的传统工艺来说,主要分为电泳层、中涂层、色漆层、清漆层。
车漆的大概处理工艺如下图(不同车企还是会有所不同的)
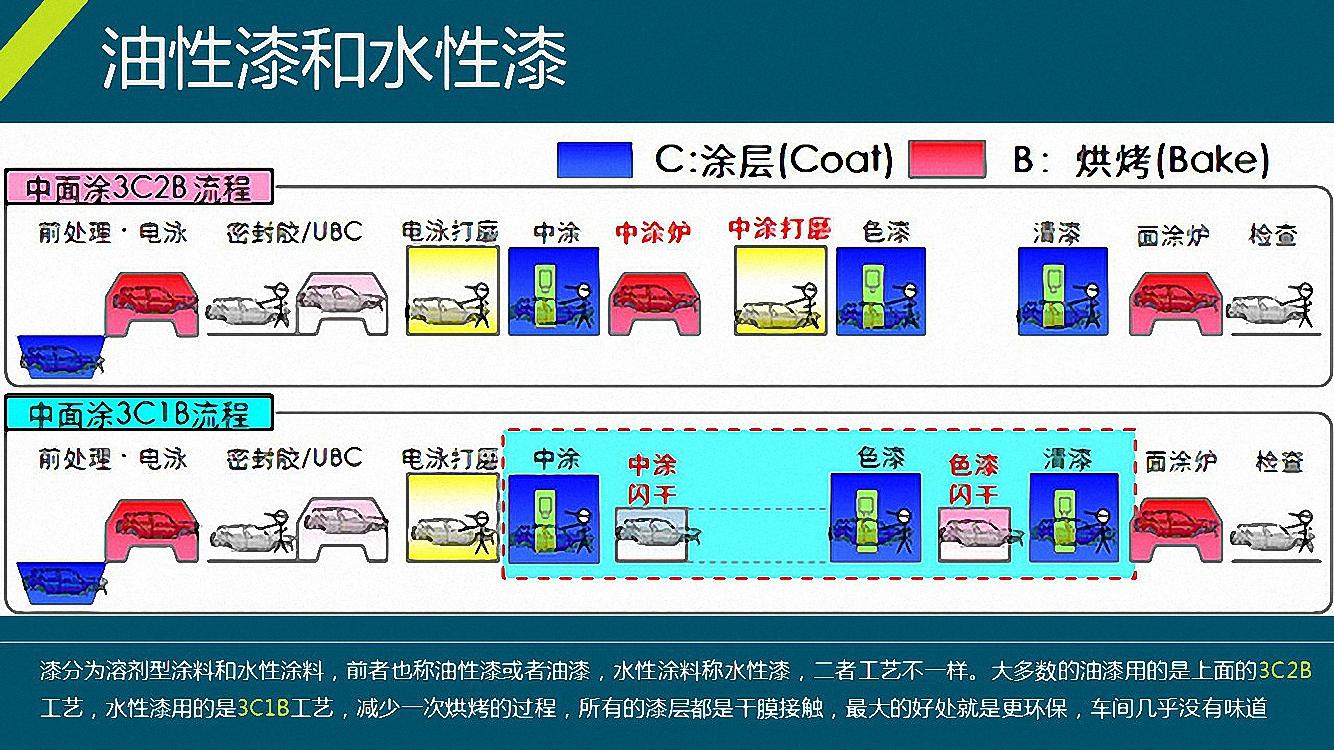
总装:
总装车间主要是完成各种总成及合件的分装、发送、车身内外饰及底盘的装配和检测、补漆和返工等工作。下图为总装工艺流程图。
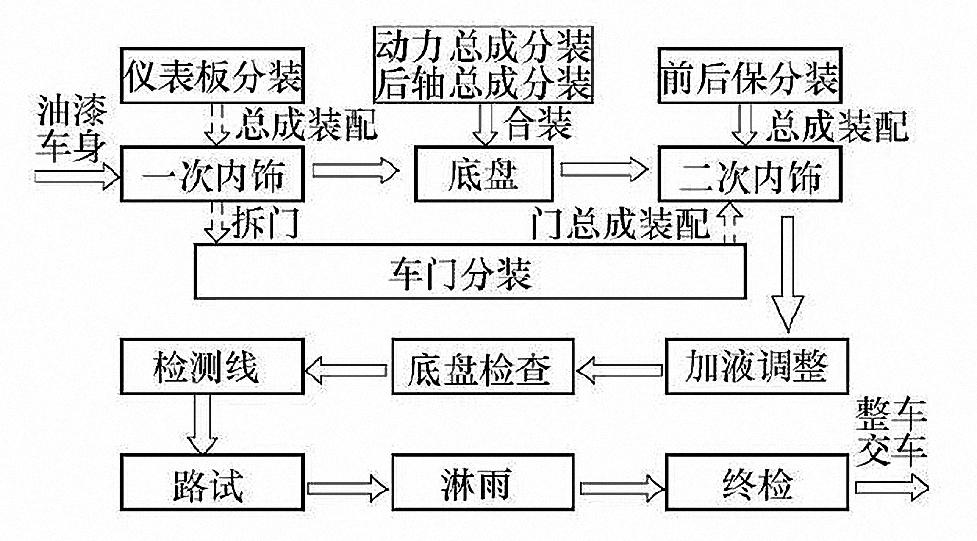
上面的一次内饰主要指的是:车门上附件、空调蒸发器、仪表板、前围隔热垫、地毯、顶棚、A/B柱护板、整车车身线束、前后风挡玻璃、雨刮器等。
上面的二次内饰主要指的是:前后保险杠、前大灯、四门护板、外后视镜、车轮、制动液、空调液、动力转向液、防冻液、清洗液的加注、四门两盖的调整、发动机预热调整、底盘件复查等。
举例:
汽车整车生产涉及到很多部分,以车身外覆盖件配合为例。
先要说明的是在在开始PPV阶段的造车以前,车身外覆盖件配合工作,应该首先需完成以下五个方面的准备工作:
1) 质量标准:主要为车身外覆盖件配合标准和整车外覆盖件配合标准;
2) 安装工具:外覆盖件安装工具的设计制造和初步调试,消除安全和人机工程问题;
3) 装配工艺:完成外覆盖件装备的初版工艺;
4) 分总成尺寸状态:外覆盖件分总成和白车身工装设备安装调试;
5) 集成状态:外覆盖件配合的状态和问题清单。
完成以上的准备工作以后,再开始工厂造车阶段阶段。
SGM工厂造车阶段分为3个步骤:
1)PPV(产品和工艺过程验证)造车
PPV造车一般在SORP 前38周开始,23周结束。主要是确认设定的工艺以及设备能否生产出达到性能要求的产品,并验证其合理性;
2)NS(非可售车)造车
NS造车一般在SORP前23周开始,13周结束。主要是验证制造系统能否满足节拍要求,保证生产过程以及产品质量的一致性;
3)S(可售车)造车PPV 造车
S造车一般在SORP前13周开始,SORP结束。主要是确认NS阶段造车结果,判定现有系统能否满足设计要求,连续稳定地生产合格产品。
以上介绍还是存在很多不足之处的,部分知识的介绍不一定准确,欢迎大家指正。
一辆汽车从研发设计到量产出售给消费者是一个繁琐且漫长的过程。这当中包括市场调研、概念设计、工程设计、样车试验、量产5个主要阶段。
而汽车的制造过程又主要分为:冲压、焊装、涂装、总装。这就是我们熟知的汽车四大工艺。接下来分四个板块介绍汽车的制造过程。
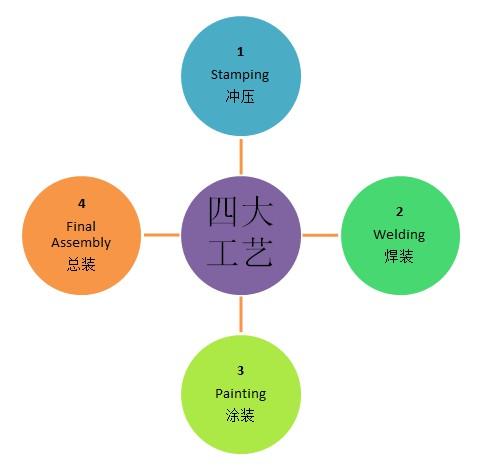
一、冲压 Stamping
冲压是汽车制造的第一步,是把金属片材通过专用模具加工成特定形状的零件。从钢厂采购回来的钢卷,经过第一次落料模具的冲压,切割加工成特定的料片形状,这个料片形状是工程师经过AutoForm等软件分析计算得出来的,这个形状一方面要保证经济性(节省材料),另一方面要保证零件的成形性。
之后,料片经过拉延成型、修边冲孔、翻边整形等模具的冲压就加工出来了白车身零件,零件需要质量人员上检具检查,对于侧围外板、翼子板、车门、发盖外板、尾门外板、顶盖等外观零件线边质量人员需要重点关注零件的外观质量,内板件相对来讲要求没有外板件高。
冲压出来的零件在满足质量、外观、尺寸要求的情况下才能存储到仓库进入下一道工序。
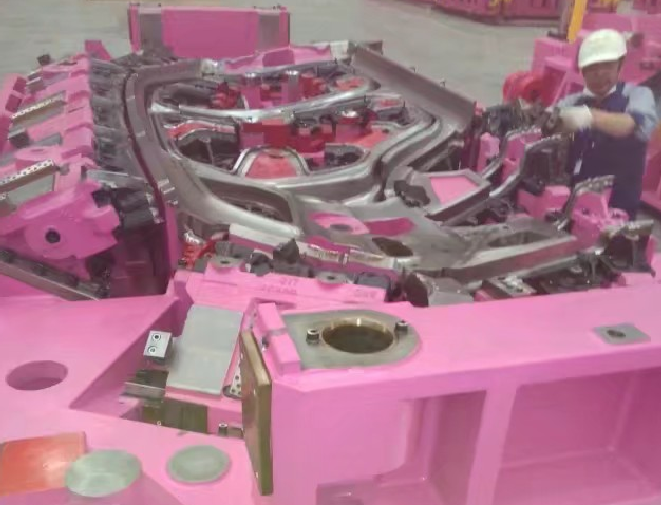
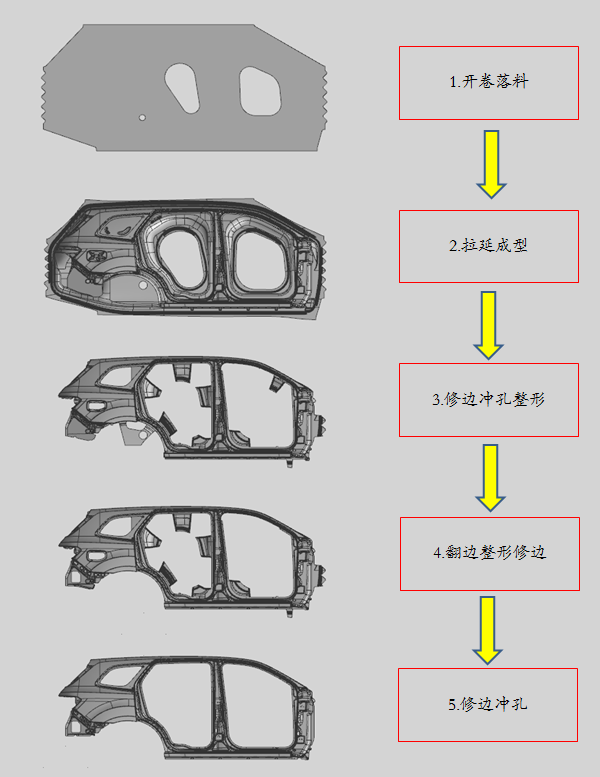
stamping processhttps://www.zhihu.com/video/1175013013202141184
stamping 2500Thttps://www.zhihu.com/video/1175013214601076736
二、焊装 Welding
冲压加工出来的都是单个的白车身零件,工人或者机器人将冲压单件放入特定的焊接工序夹具上,焊接机器人或者工人通过焊枪把不同的冲压零件焊接成分总成,分总成然后焊接成总成,总成最后焊接成完整的白车身。
主要的焊接总成有:发动机舱总成、地板总成、侧围总成、前后门总成、尾门总成、发盖总成等。
总成的打胶、包边工序也是焊接工程师负责,目前常见的包边实现方式有:包边机器人和包边模具两种。
焊接完的分总成、总成、白车身是需要进行焊接质量检测,常见的焊接质量问题有:焊渣、虚焊、过焊等。
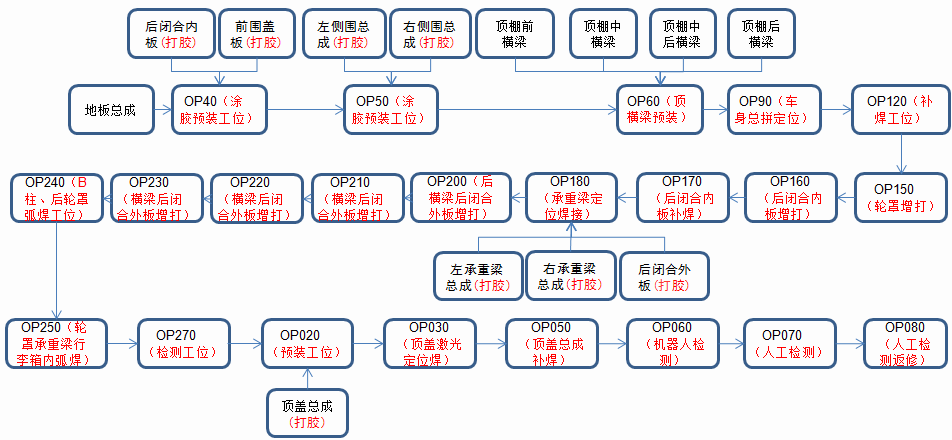
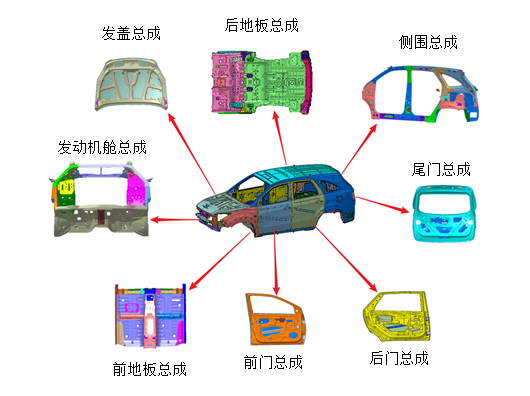
welding processhttps://www.zhihu.com/video/1175013495035416576
三、涂装 Painting
从焊装车间出来的白车身会进入涂装车间,白车身在涂装车间主要是经过电泳、中漆、面漆三个处理过程。
在白车身进行电泳之前需要进行杂质清理、油污清理、磷化处理等,目的是提升电泳漆与白车身的附着力。电泳的主要作用是白车身防腐,电泳完后经过烘干处理进入下一工艺流程。
电泳烘干完的白车身会进行喷密封胶、贴阻尼板、喷防石击涂料等处理,然后进行清理后进行喷中漆,车身喷中漆处理完之后,也需要进行烘干处理。
中漆烘干处理完后,需要进行打磨抛光清理,然后进行白车身面漆喷涂处理,在这之后进行烘干处理,然后会进行最后一轮的检查修复抛光处理。然后将车身输送到总装车间。
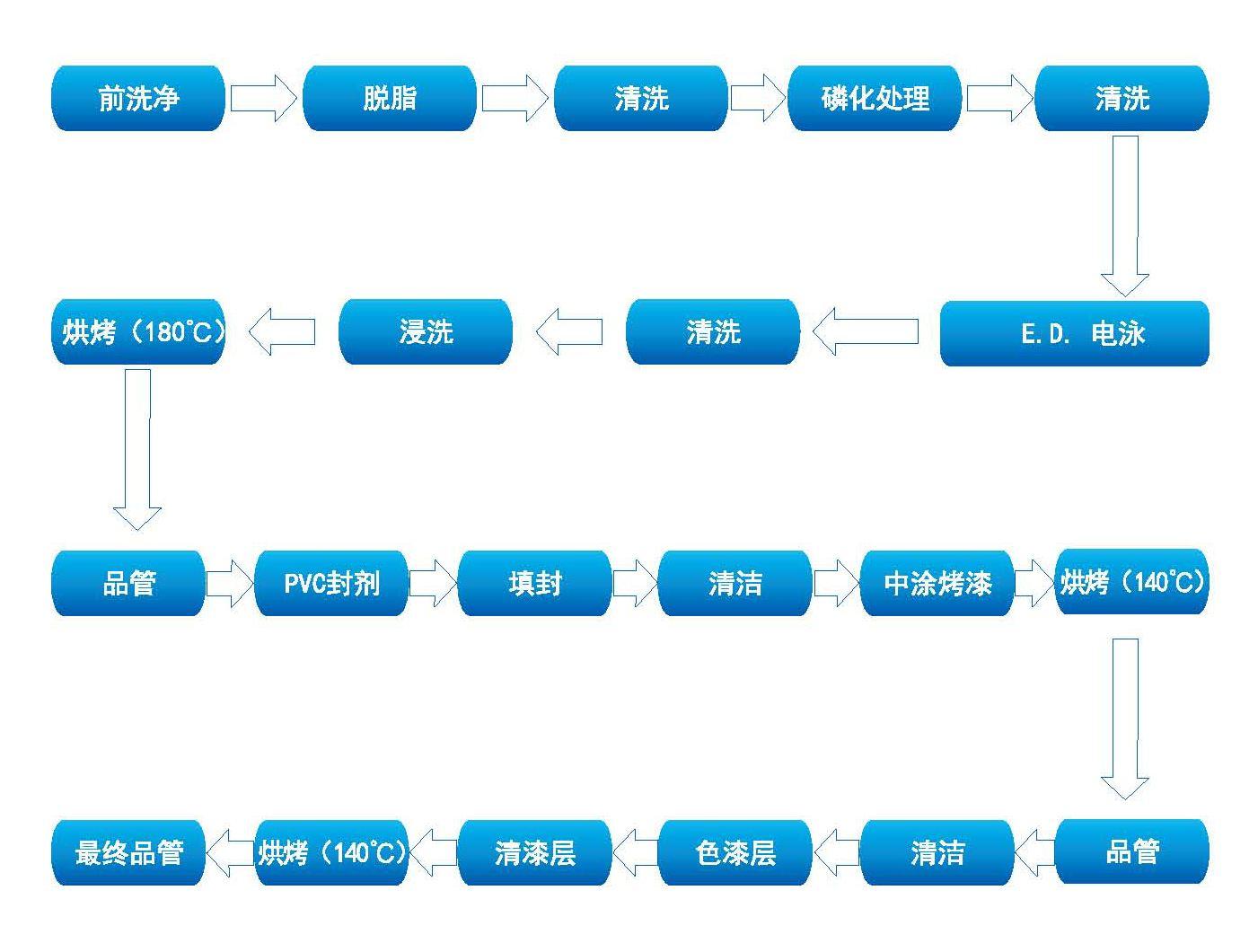
painting processhttps://www.zhihu.com/video/1175013743674748928
四、总装 Final Assembly
总装是汽车制造四大工艺的最后一环。总装线主要有内饰线、底盘线、外饰线等。从涂装车间出来的车身进入总装线,会进行线束、车门、安全气囊、ECU、仪表板、发动机、前后桥、轮胎等各种内饰、外饰、电子电器等零部件的安装。
燃油、润滑油、清洁剂、冷却液、制动液、防冻液等油液也都会在这个过程当中加注。
总装完成的整车需要经过最后的检测,主要的检测项目有:四轮定位检测、前照灯检测、制动性能检测、排放检测、淋浴检测、道路检测等。
至此,一辆合格的整车就可以运送到各地4S店出售给消费者了!
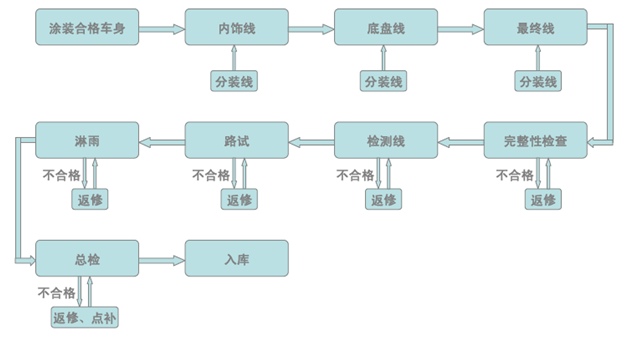
final assembly processhttps://www.zhihu.com/video/1175013904522113024
希望这个回答能让更多的读者了解汽车的制造过程,限于个人能力,有不恰当之处,请多多指教。
部分图片视频来自网络,侵删。
长文多图预警。(收藏的各位大哥双击一下屏幕点个赞吧)汽车生产制造的流程一般分为4+1:就是四大工艺+质保检查。
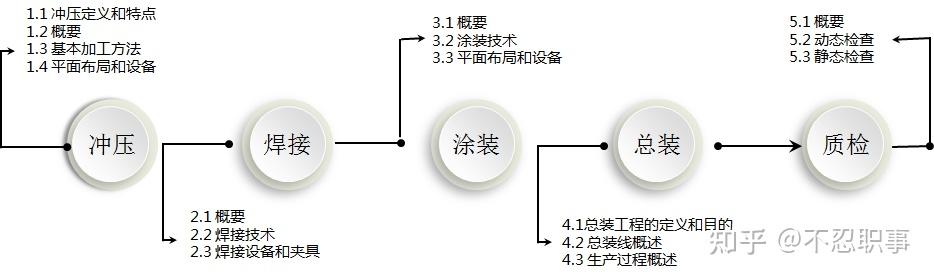
冲压是一种金属加工方法,它是建立在金属塑性变形的基础上,利用模具和冲压设备对板料施加压力,使板料产生塑性变形或分离,从而获得一定形状、尺寸和性能的零件(冲压件)。
冲压的特点产品尺寸稳定,精度高,重量轻,刚度好,互换性好,高效低耗,操作简单,易于实现自动化。 据统计,汽车上有60%–70%的零件是用冲压工艺生产出来的。因此,冲压技术对汽车的产品质量、生产效率和生产成本都有重要的影响。
冲压的零件一般为400左右,整车厂自制零件数量30~40件,其余零件均为供应商采购。(不同工厂会有较大差异)
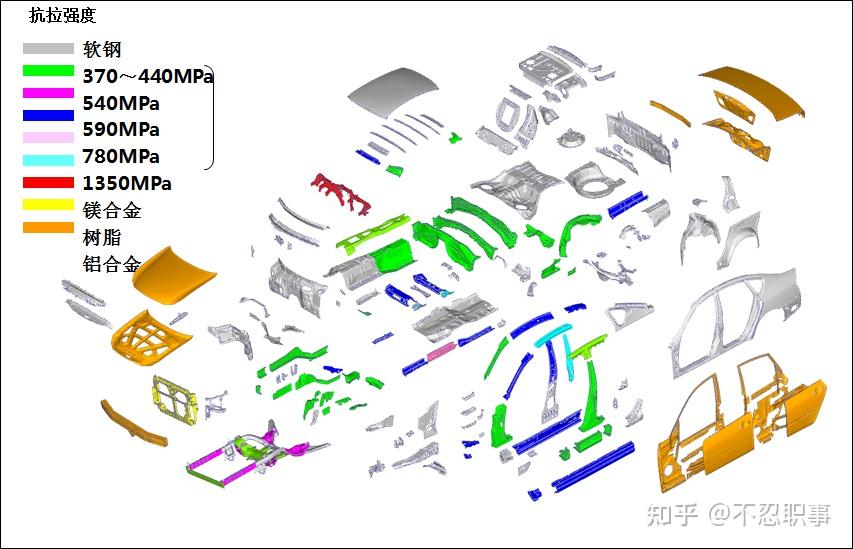
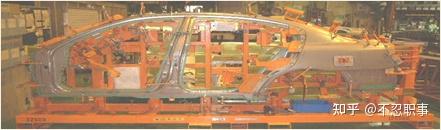
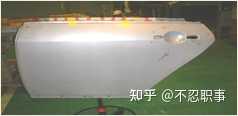
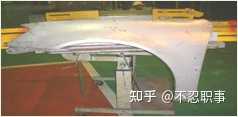
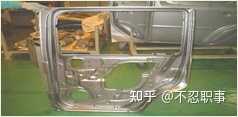
冲压加工的特点:
- 冲压加工适用于大批量生产。 具有高的生产效率 (短的生产时间). 生产速度: 串联线 = 5 to 8 件/分. 多工位线 = 10 to 15件/分.
- 钢板相对于其他材料而言,较便宜, 强度高且较轻便. 非常符合汽车性能的要求.
- 金属冲压可以满足汽车零部件的要求: 漂亮的外观, 高尺寸精度, 高再现性.
冲压加工方法可分为6种:
- 落料
- 拉延
- 修边,冲孔
- 翻边
- 整形
- 包边
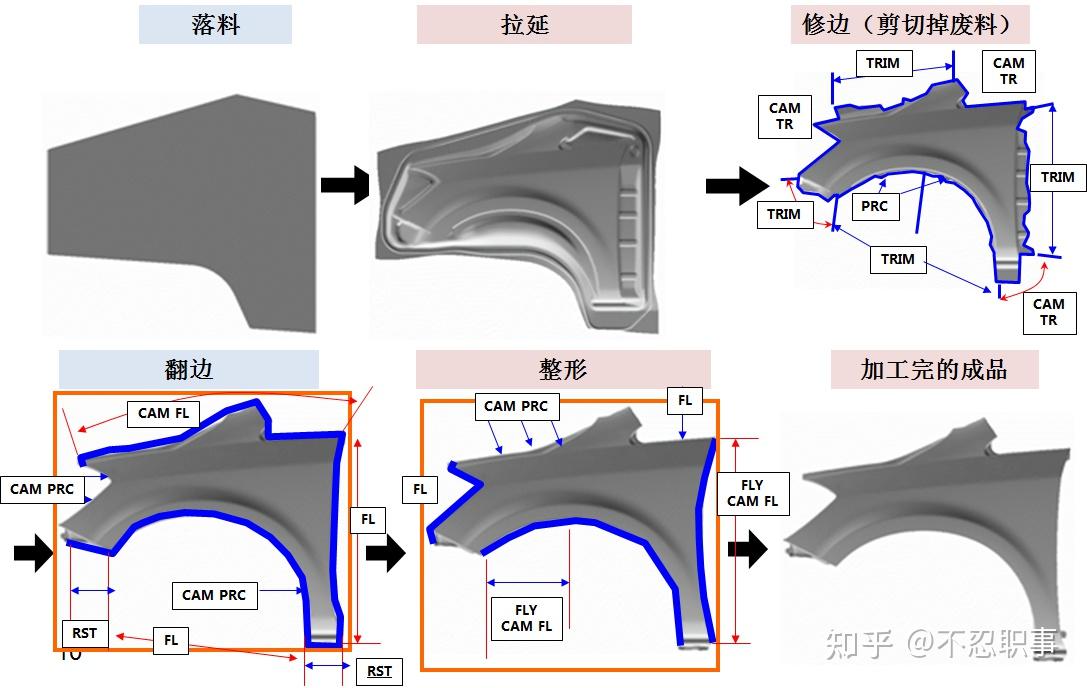
1.3.1落料
在这个工序中,钢材供应商运送的钢卷被剪切成板料,也就是各个复杂曲面的汽车钣金造型都是从平板的钣金开始的.
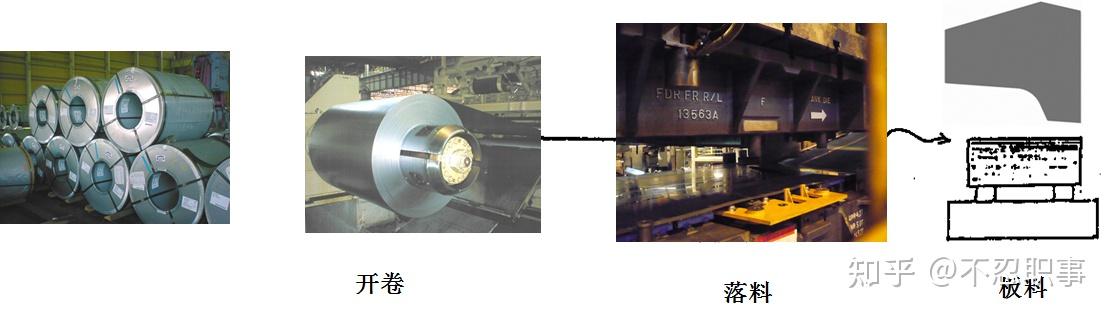
1.3.2拉延
也称拉深、拉伸、压延等,是指利用模具,将冲裁后得到的一定形状平板毛坯冲压成各种开口空心零件或将开口空心毛坯减小直径,增大高度的一种机械加工工艺。用拉深工艺可以制造成筒形、阶梯形、锥形、球形、盒型和其他不规则形状的薄壁零件。
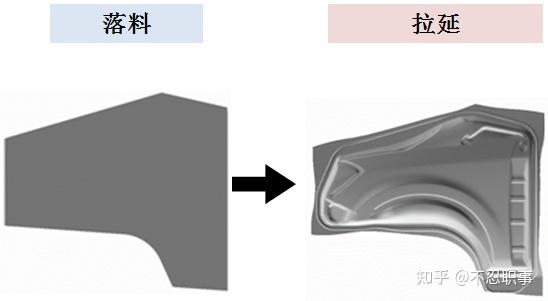
1.3.3修边,冲孔
修边是将为保证拉深成形而在冲压零件的周围增加的工艺补充部分和冲压件内部增加的工艺补充部分冲裁剪切掉的冲压工序。冲孔是在需要的位置根据不同的设计及工艺要求冲出来的孔。
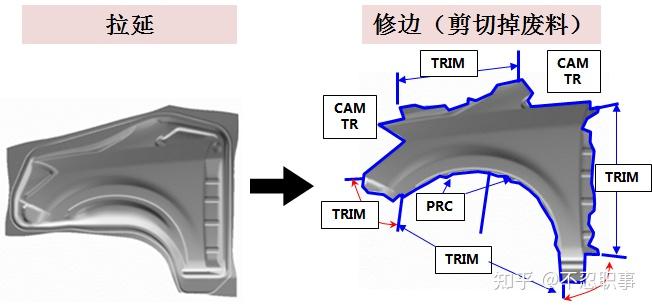
1.3.4翻边
翻边指的是在坯料的平面部分或曲面部分上,利用模具的作用,使之沿封闭或不封闭的曲线边缘形成有一定角度的直壁或凸缘的成型方法。
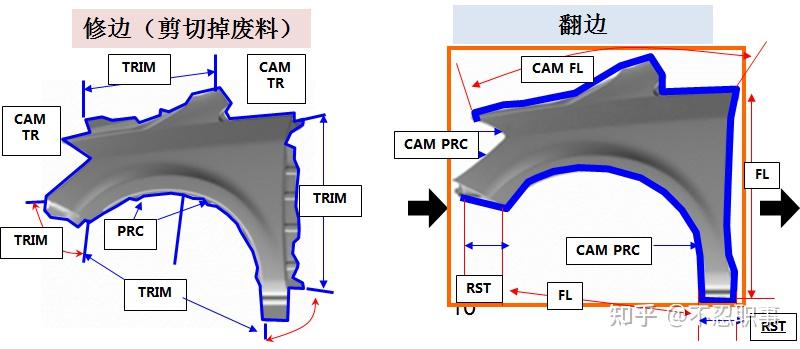
1.3.5整形
为了提高已成形零件的尺寸精度或获得小的圆角半径而采用的成型方法。
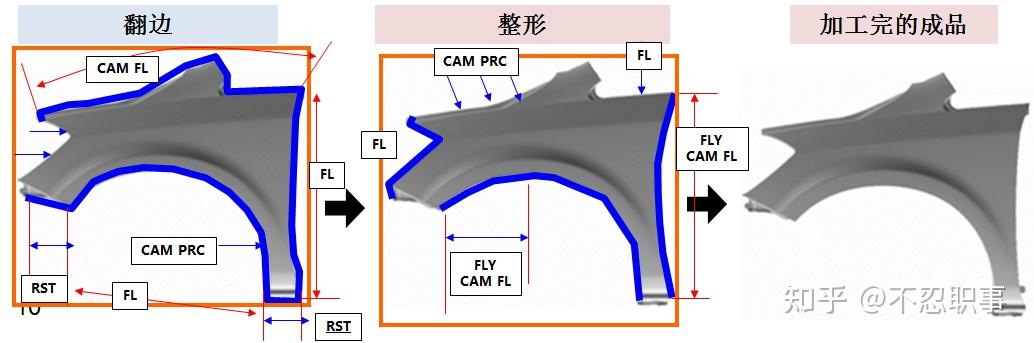
1.3.6包边
包边是一种 在板料边缘进行折叠以达到强度增强及润滑效果或者装配另外的零件的加工方法. 在装配的时候, 装配的零件通过180度弯曲紧紧的折叠在一起. 通常, 包边工序是在焊接车间进行。
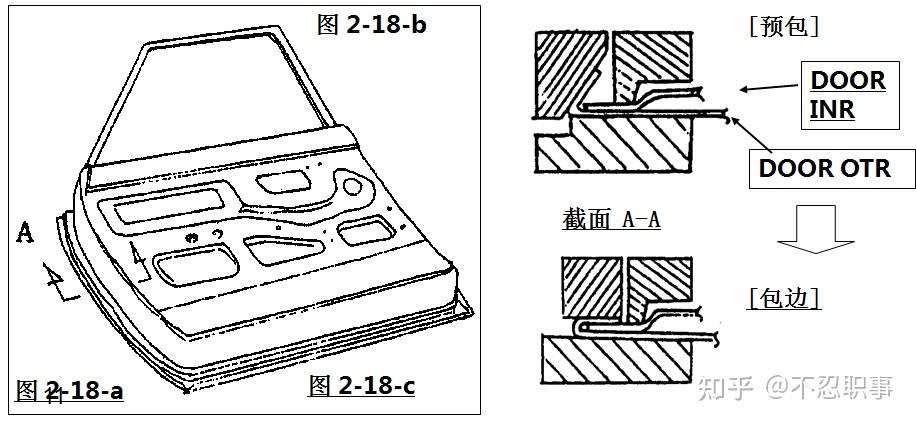
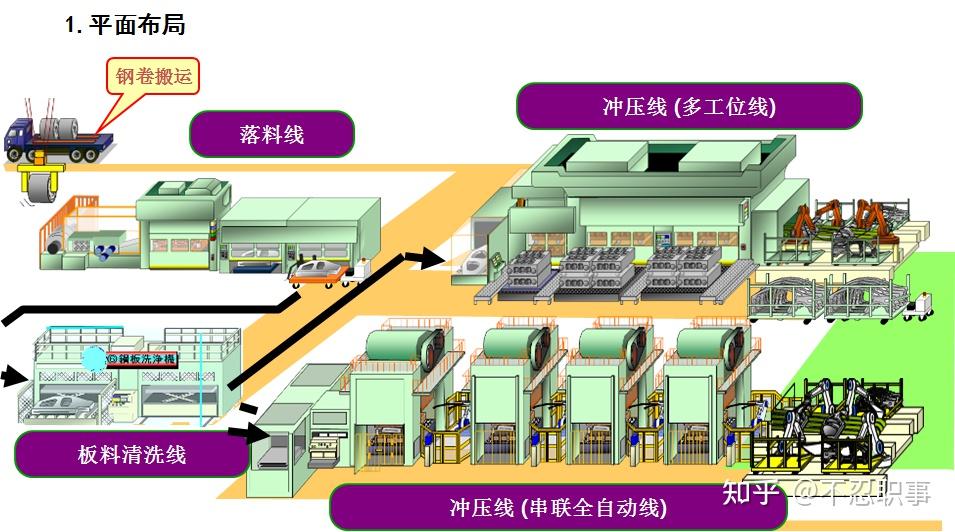
1.4.1设备·落料线
这是一种将钢材供应商交付的卷料剪切成板料(片材)的自动冲压线。压力机的压力一般是 200 ~700T ,冲压能力一般是 30 to 100 SPM (高速转动).卷料在设定好长度(剪切尺寸)后进行自动剪切。
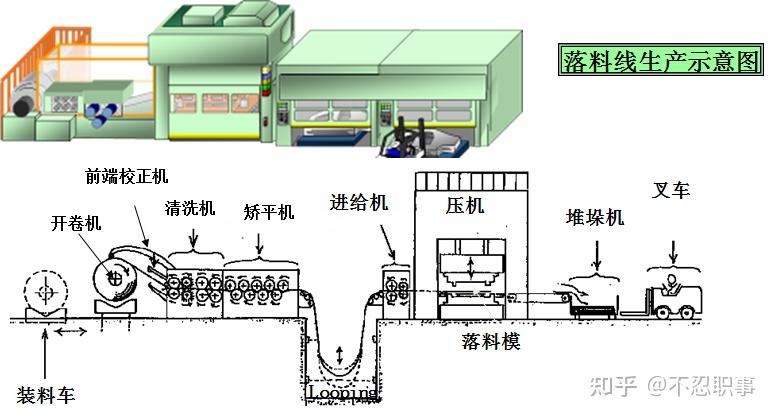
1.4.2设备·冲压线 (串联全自动生产线)
一条线有4~5台压力机.零件的上料/下线都是通过机器人自动操作的线体被称为串联全自动生产线(Tandem full automatic line)
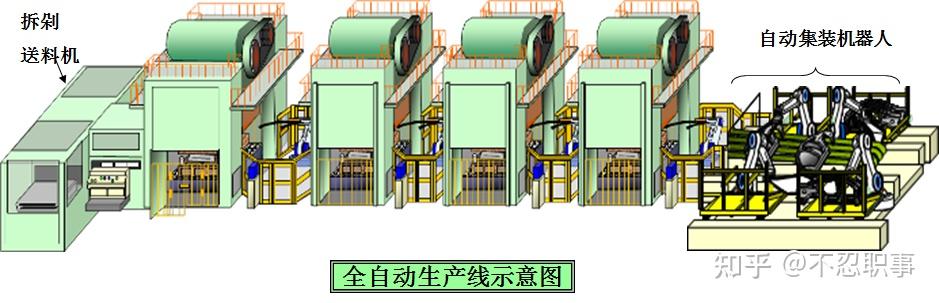
1.4.3设备·冲压线 (多工位全自动生产线)
多工位生产线不仅有多个冲压工位的模具,还有工位之间的传送装置。传统的操作需要多个冲压设备,然而,在多工位生产线中可以在一台冲压设备上完成。多工位生产线的引进使人工劳动力减少,占地面积减小。另外,多工位生产线大大提高了生产速度。
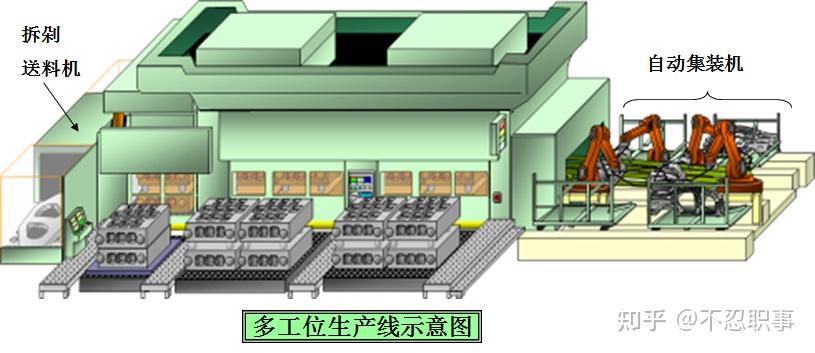
车身装配工艺是通过焊接方式或螺栓螺母等紧固由冲压车间或零部件供应商生产的各种零件,进行加工形成白车身总成,并送入涂装车间。
零部件数量约350-400件(冲压自制零件30-40件,供应商零件数量约为1000件,装配形成约350个分总成,焊点数量为1500左右,用螺栓进行密封于紧固。),装配形成车身,焊点数量约为3000-4000,应用螺栓、螺母进行密封于紧固。
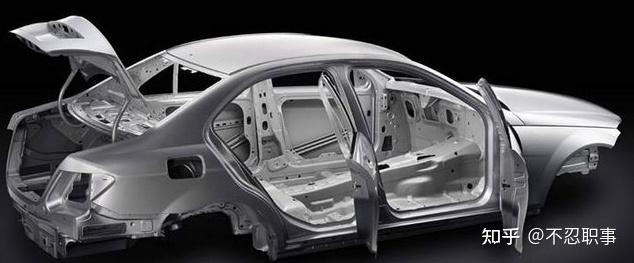
车身的基本构成:
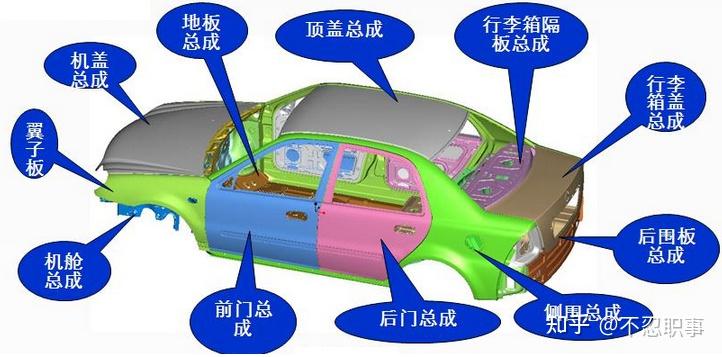
- 焊接 通过施加热量融化焊材使得零部件结合一起。
- 粘接 通过粘接剂将板材粘接在一起。
- 褶边(包合) 通过使外板折叠(包进)内板里面使两个板材结合一起。
- 紧固 采用螺栓、螺母使得两个板材紧固一起。
2.1焊接
焊接是通过加热或者加压,或者两者并用;加或不加填充材料;使两分离的金属表面达到原子间的结合,形成永久性连接的一种工艺方法
点焊、弧焊、激光焊接被应用于车身不同部位焊接,点焊是车身大部分部位焊接所采用的方式。弧焊被应用到由于车身结构限制无法使用点焊进行焊接的部位,激光焊接被应用到有限部位如车顶和车门槛焊接。
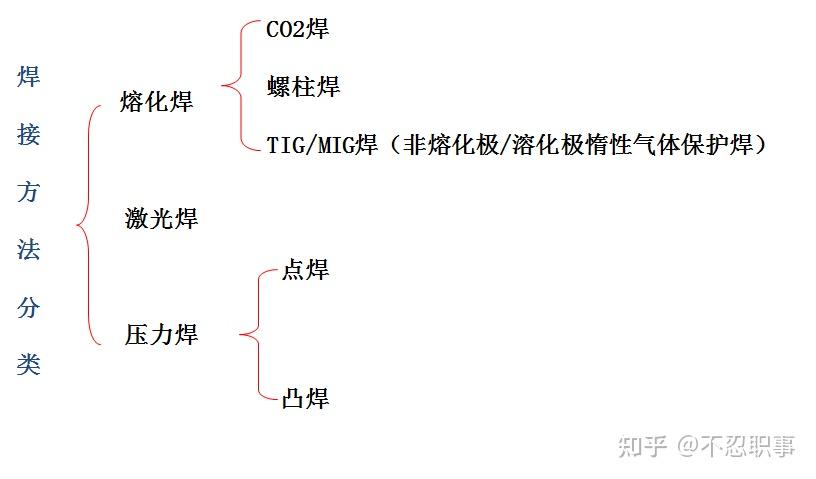
2.1.1焊接方法·CO2气体保护焊方法的原理
CO2气体保护焊是采用CO2气体作为保护介质,焊接时,CO2气体通过焊枪的喷嘴,沿焊丝的周围喷射出来,在电弧周围形成气体保护层,机械地将焊接电弧与空气隔离开来,从而避免了有害气体的侵入,保证焊接过程的稳定以获得优质的焊缝,其工作原理如图:
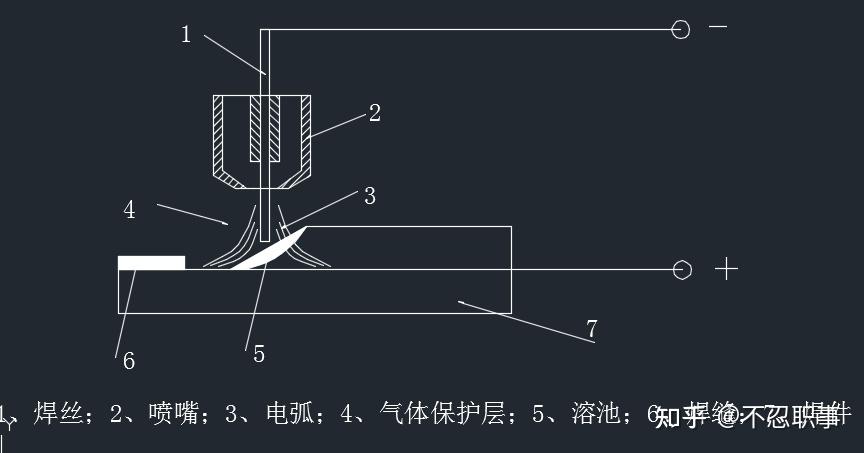
2.1.2焊接方法·螺柱焊焊接原理和过程
开始时先将螺柱放入焊枪的夹头里并套上套圈,使螺柱端与工件(母材)接触(图1)按下开关接通电源,枪体中的电磁线圈通电而将螺柱从工件拉起,随即起弧(图2)。电弧热使柱端和母材熔化,由时间控制器自动控制燃弧时间。在断弧的同时,线圈也断电,靠压紧弹簧把螺柱压入母材熔池即完成焊接(图3)。最后形成焊接接头(图4)
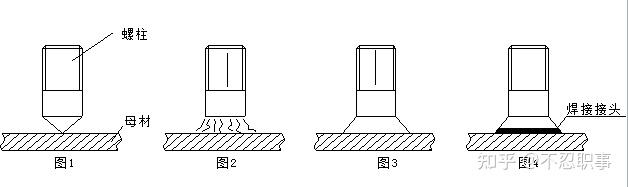
2.1.3焊接方法·电阻焊的焊接过程
一个完整的点焊形成过程包括预压程序,焊接程序,维持程序,休止程序。在预压阶段没有电流通过,只对母材金属施加压力。在焊接程序和维持程序中,压力处于一定的数值下,通过电流,产生热量熔化母材金属,从而形成熔核。在休止程序中,停止通电,压力也在逐渐减小。
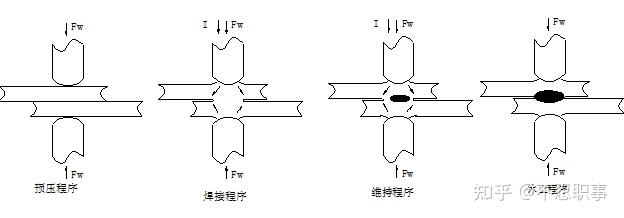
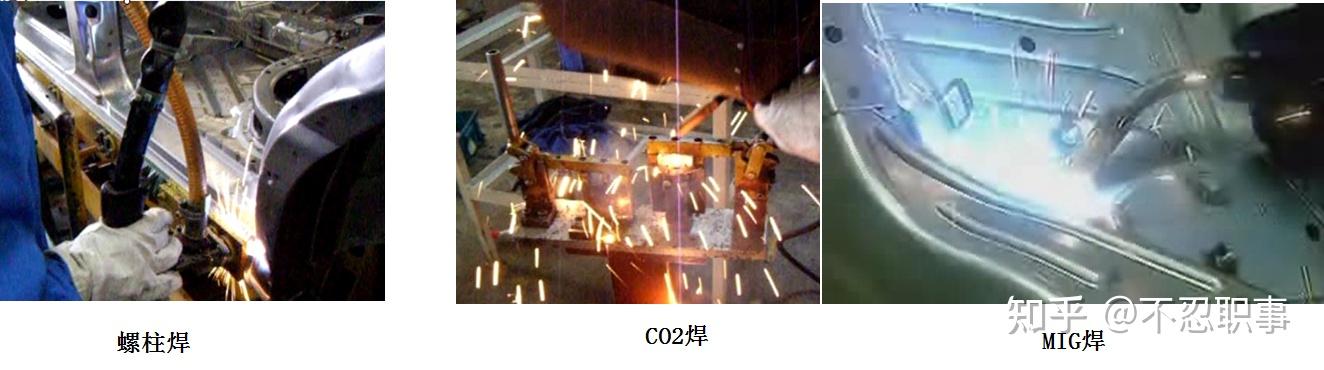
2.2粘接
车身上的粘接工序目前分为两类,树脂密封材料和结构粘接剂。通过在加强板和外板之间填充树脂密封材料能够阻止外板变形和接触。结构粘接剂应用于点焊不能施加的部位。
2.3褶边(包合)
这种方法这种应用于外板件诸如车门、引擎盖等,目的使加强板和外板结合一起而没有留下焊接痕迹。可应用包合的零件有车门、引擎盖、行李箱盖、后门等。
2.4紧固
安装车门、引擎盖、FR FENDER和其它部件到车门。—将铰链用螺栓和焊接螺母拧紧。
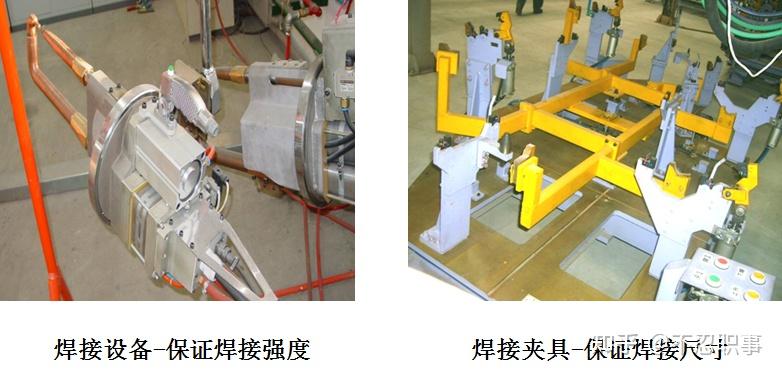
2.3.1悬点焊机
悬挂式点焊机简称悬挂焊机,是电阻焊点焊的一种。电阻焊是工件组合后通过电极施加压力,利用电流通过接头的接触面及邻近区域产生的电阻热进行焊接的方法,分为点焊、凸焊、对焊、滚焊。
2.3.2螺母焊机
螺母输送机是配合螺母固定式点焊机使用的一种机器,该机器利用磁场震动的原理将螺母进行选料并输送至点焊位置上。
2.3.3CO2焊机
二氧化碳气体保护焊是焊接方法中的一种,是以二氧化碳气为保护气体,进行焊接的方法。在应用方面操作简单,适合自动焊和全方位焊接。在焊接时不能有风,否则会产生气孔或其他焊接缺陷,适合室内作业。
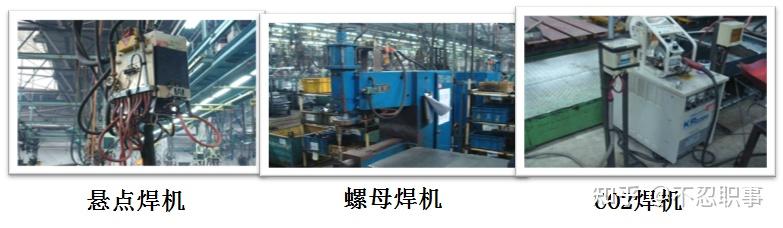
涂装的作用有三个:
- 1、保护作用:由于汽车几乎全部由钢板组成,因此,涂装可防止其产生腐蚀及保护车体。
- 2、装饰作用:通过涂装可以起到美化外观的作用。
- 3、使用价值的提高:漂亮的涂装(色泽、鲜映度等)可提高用户的购买意愿。
涂装的特点:
- 规模生产,及设备高自动化率,汽车外板可使用自动化涂装
- 汽车作为大规模生产产品,针对其大型而复杂的形状有很多涂料规格。
- 对涂膜的防腐、外观、耐久性要求非常高, 涂膜性能必须适用与汽车使用的各种环境。
一般涂层的结构:
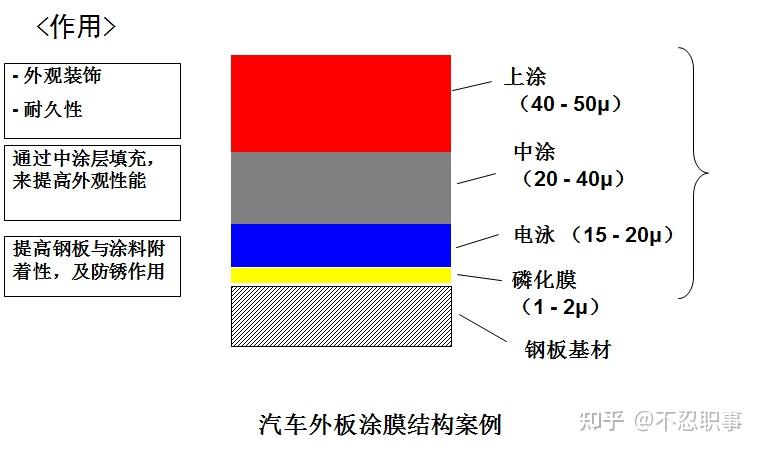
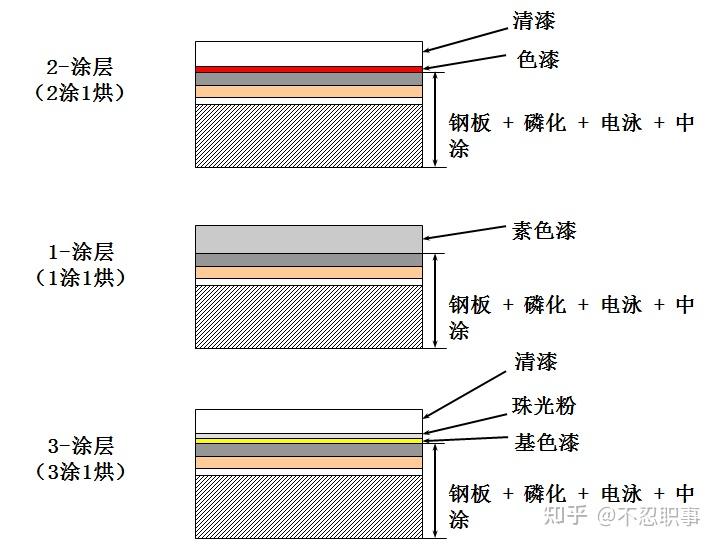
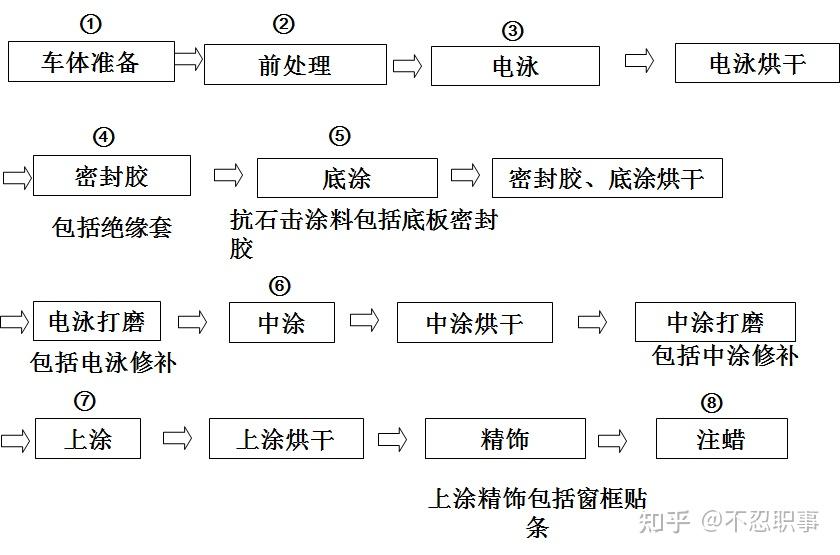
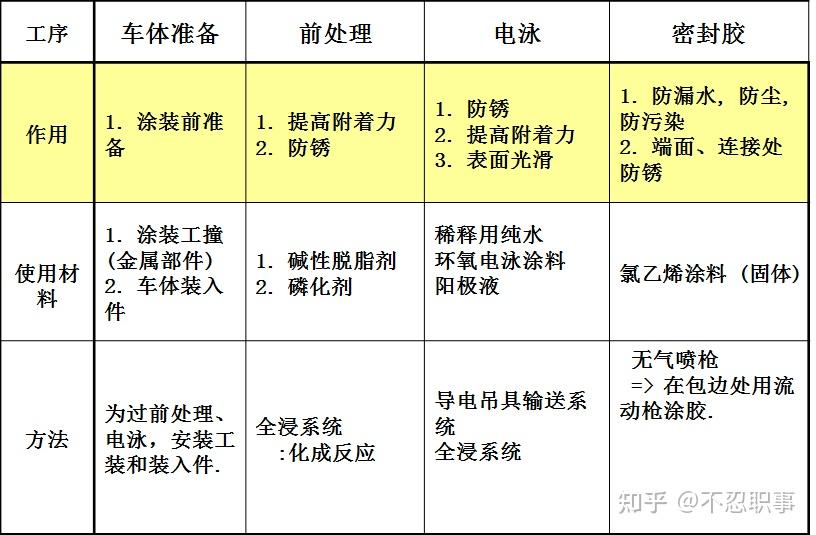
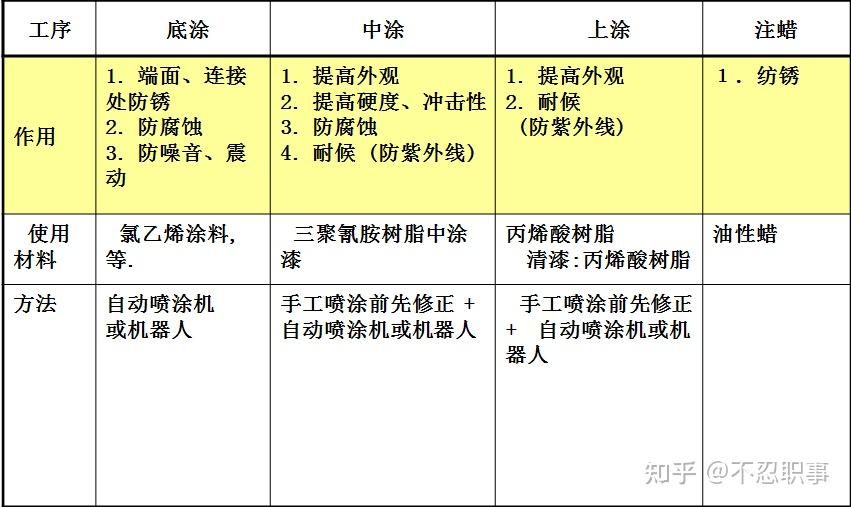
3.2.1.车体准备工序
- 零件安装 (将零件安装在车体内部保持同时涂装.)
- 工装安装 (安装工装已保持车门张开.)
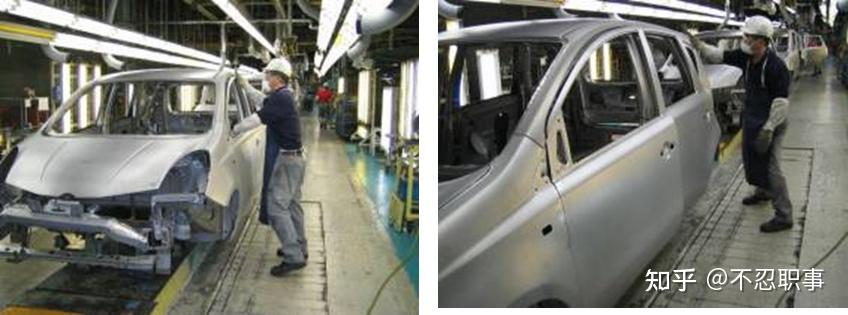
3.2.2前处理工序
- 脱脂 (去除车体附着的油脂等赃物.)
- 磷化处理 (生成磷化膜以提高与电泳涂膜的附着力.)
- 将车体浸沫在冲洗液里. (全浸系统)
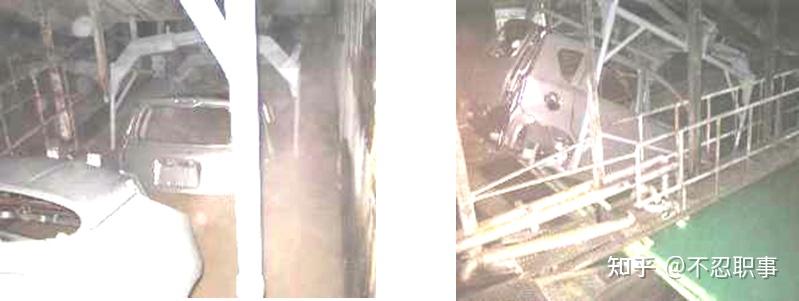
3.2.3电泳工序
将车体浸入电泳槽,车体作为阴极,槽体周边阳极向车体通电,从而在车体上通过电沉积产生涂膜(阴极电泳),给汽车内板和外板提供防锈能力.
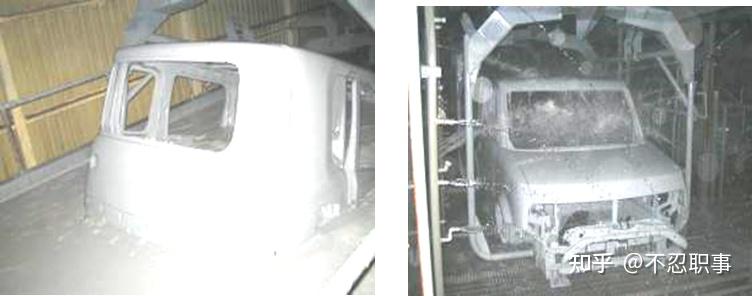
3.2.4密封胶工序
用胶枪在钢板连接处涂上密封胶. 根据外观需要用刷子和刮铲进行修整. 作用是美化外观、防水,防锈,防尘.
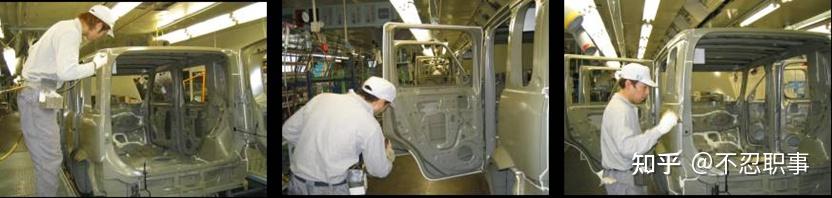
3.2.5底涂,抗石击涂料工序
用机器人、自动喷涂机或手工喷枪在地板下涂上底涂涂料、 抗石击涂料(主要作用是防噪音防震动防止被石头击穿油漆产生生锈.)
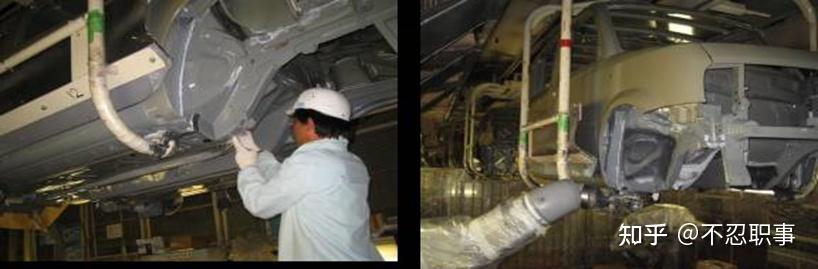
3.2.6喷涂
自动喷涂机在车体外板喷涂合适亮度和色调的涂料。
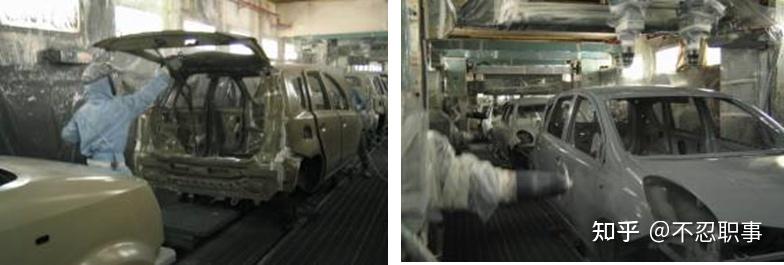
3.2.7注蜡
用配置特定喷嘴的空气喷枪在内板的封闭区域喷涂. 门底内外板夹心区域等,提高车体内框防锈力。
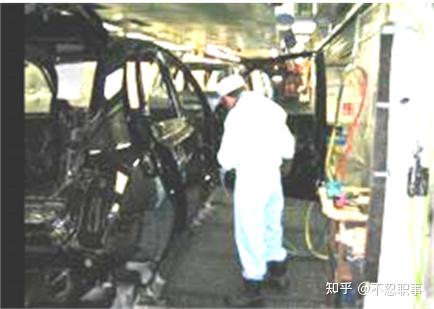
3.3.1涂装设备平面布局
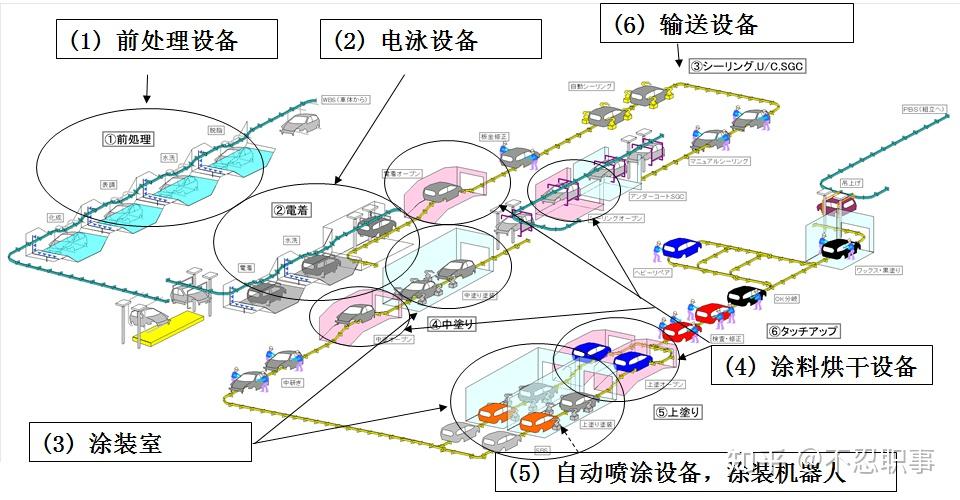
3.3.2.前处理设备
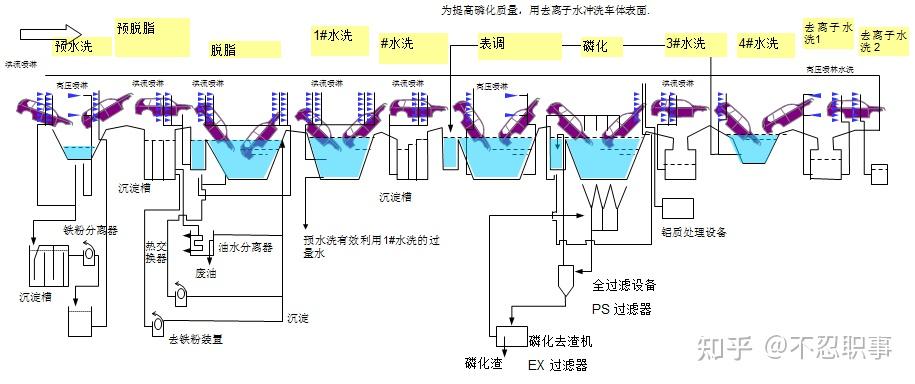
3.3.3电泳设备
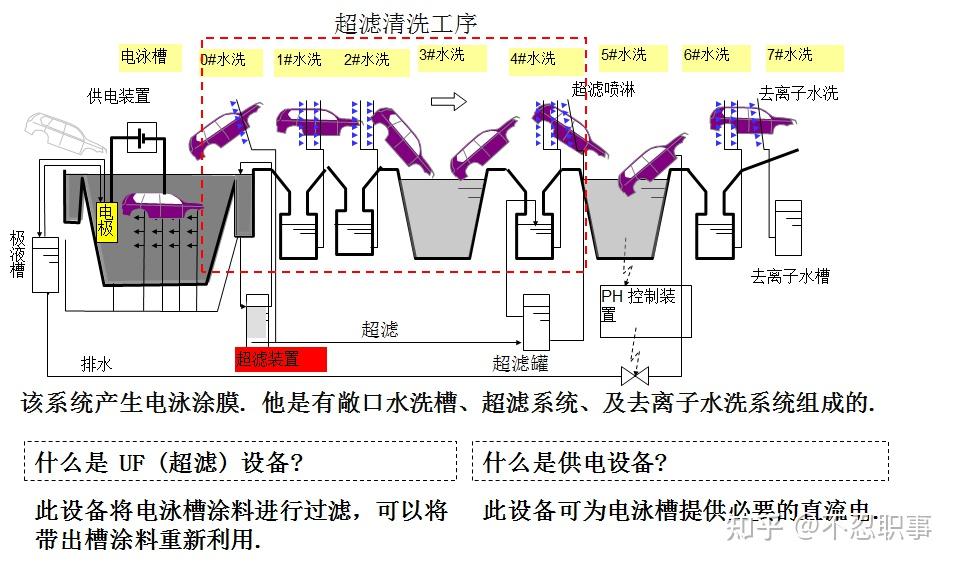
3.3.4涂装室
由保证涂装质量的空调送风设备、废气处理设备、及过喷涂料处理的水循环设备组成.
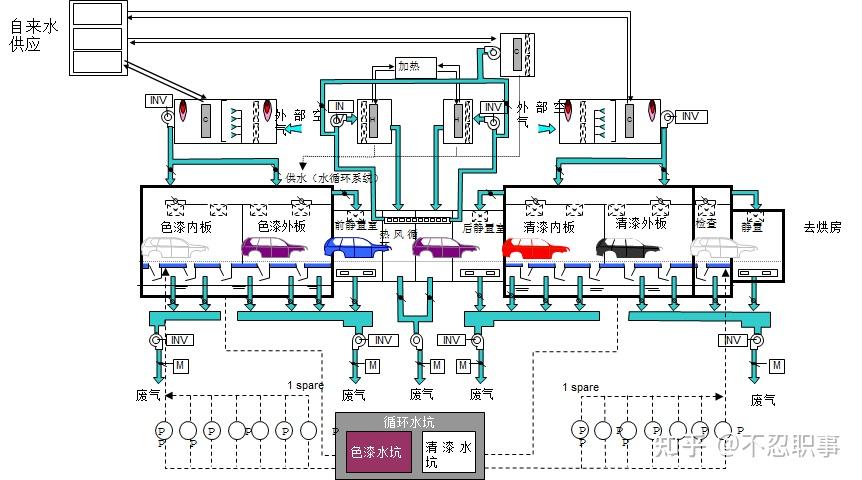
由恒温、恒湿、风速稳定设备组成,以保证涂装质量,防止 涂装不良、流挂、不匀、灰尘和颗粒等。
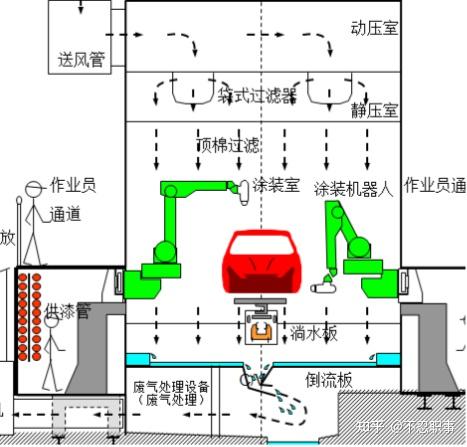
3.3.5涂装烘房
确保涂膜烘烤后质量平整光滑。 同时, 烘房里为燃净的废气不用引起设备火灾.
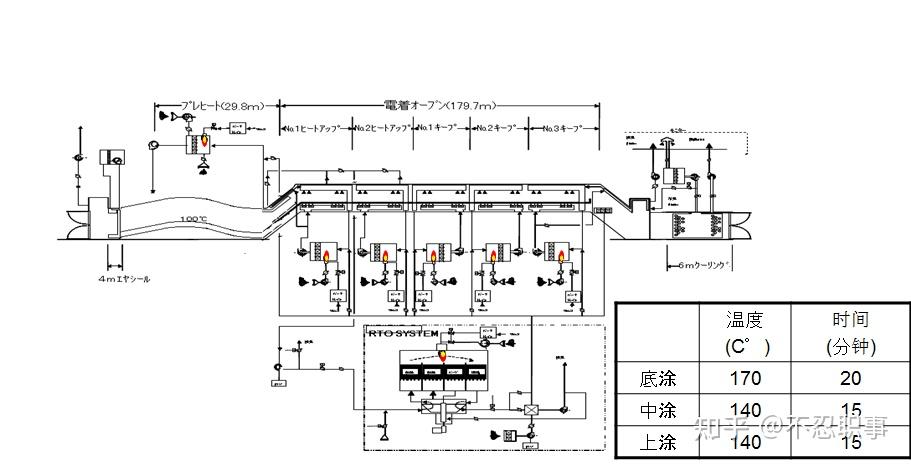
总装是指完成商品(成品车)的最后组装的工序的工程简称。主要作业是将车身、底盘和内饰等各个部分组装到一起,形成一台完整的车 。
所谓装配就是将各种零件、部件、合件或总成按规定的技术条件和质量要求联接组合成完整产品的生产过程。
总装线体普遍使用传送带装:车架或车身安放在传送带上,以固定速度行进,装配工人同时进行装配。
4.2总装工艺
总装工艺一般分为六大类:
- 螺栓、螺母紧固
- 粘接作业
- 加注作业
- 卡扣连接
- 管路连接(软管、制动硬管、空调管路)
- 线束插接
4.2.1螺栓、螺母紧固
俗称打螺丝,螺钉、螺栓联接是机械装配的基本方法,它约占汽车装配作业工作量31%,个别部位的螺纹联接采用手动扳手,较普遍的是采用风动扳手或电动扳手以及电动螺丝刀等。
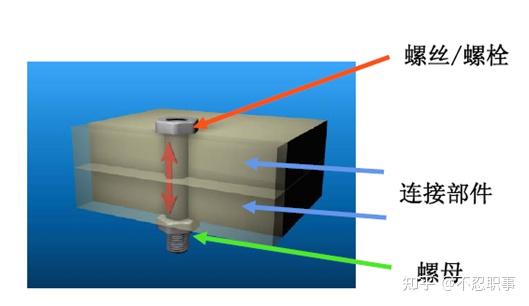
4.2.2粘接
需粘接的零部件,内饰件一般有衬垫、隔音材料、车门内装饰护板,外饰件一般有挡风玻璃、三角窗、车灯、标志、车门外装饰板等。粘接方法:小件预先在车身上涂粘接剂 ,大件则在需要装在零件上直接涂粘接剂。
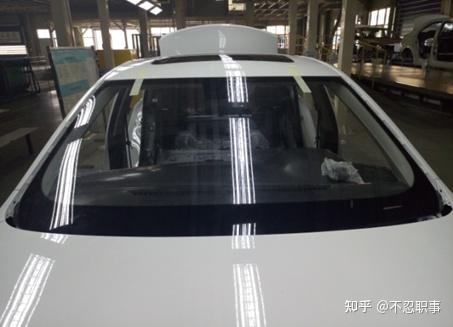
4.2.3加注
装配时将发动机机油、变速器齿轮油、散热器冷却液、制动液、动力转向液压油、空调制冷剂、挡风玻璃洗涤液、燃油等各种液体装入各总成件内的方法。
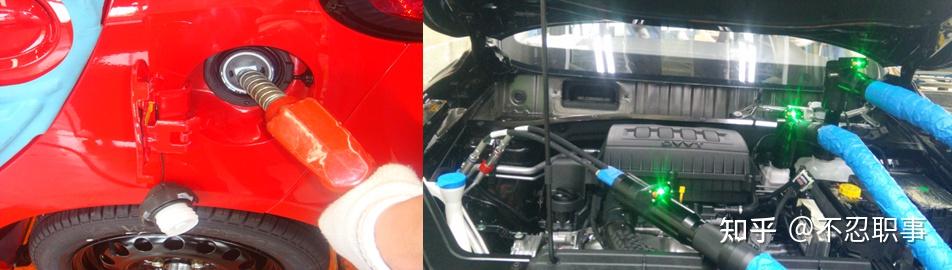
4.2.4卡扣
装配时,通过安装在零件卡座上的卡扣,与车身上对应的安装孔对接,实现零件装配在车身相应位置上。多用于内饰件及线束的装配。
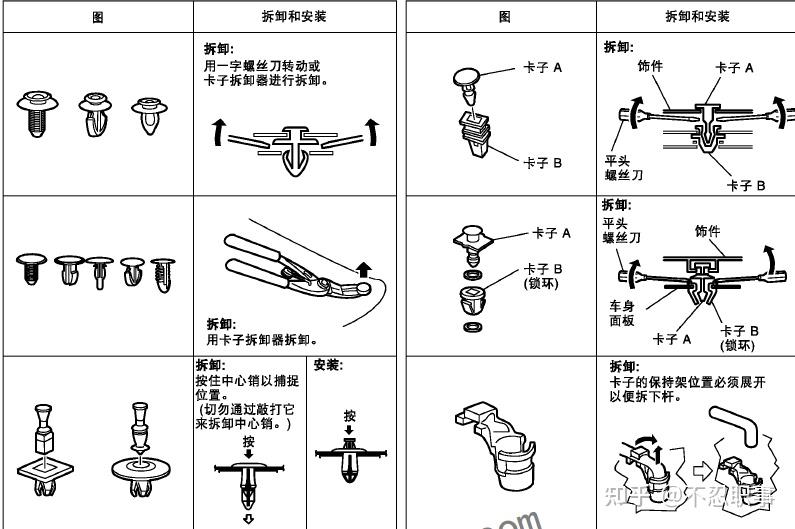
4.2.5管(软)路连接
卡箍、环箍连接法通过钢带式、钢丝式、蜗杆传动式等类型的卡箍,起到束紧零件的作用。多用于油、气、水管路的装配,在软管和硬管插接后起到固定作用。
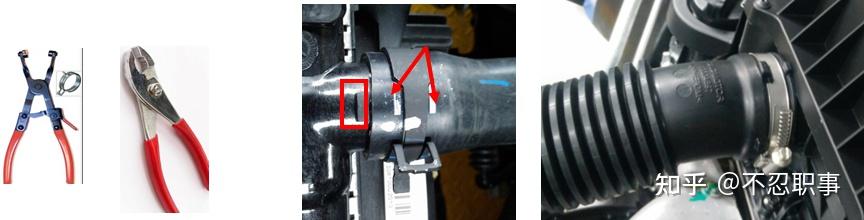
4.2.6插接法
多用于电器件线束的装配。通过线束之间、线束与汽车用电装置之间设计成公母两端的插接,实现整车电路的接通。
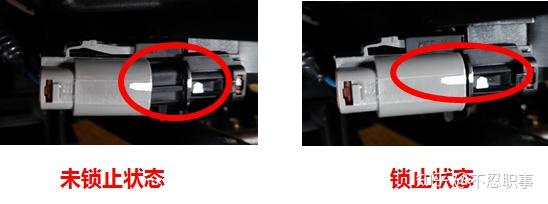
43总装平面布局
总装线体一般包括整车装配线(工艺链,由多台电动机驱动)、车身输送线、储备线、升降机等。 汽车装配线一般是由输送设备(空中悬挂和地面)和专业设备(如举升、翻转、压装、 加热或冷却、检测、加注、螺栓螺母 紧固设备等)构成的有机整体。
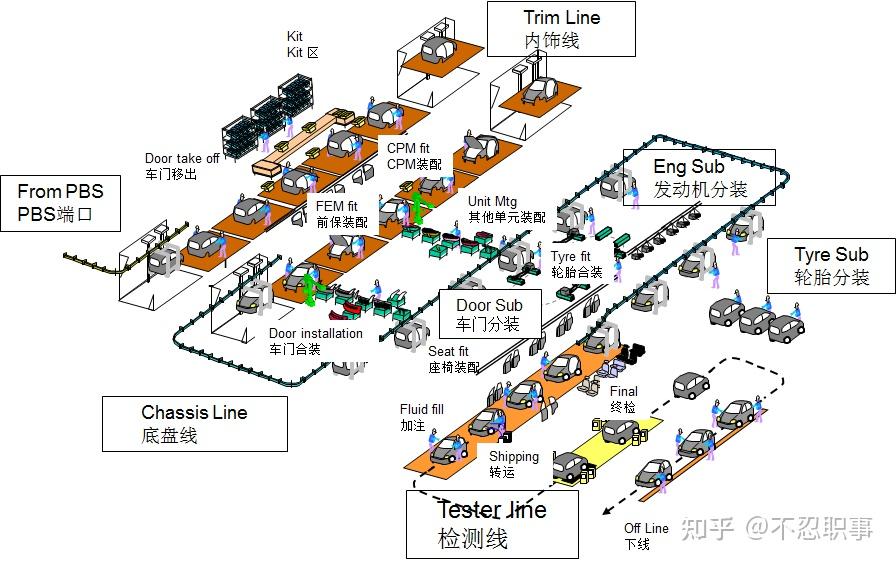
内饰线:一般包含移出车门,布配线束,装配机舱零件,内外饰零件,以及风窗玻璃等。
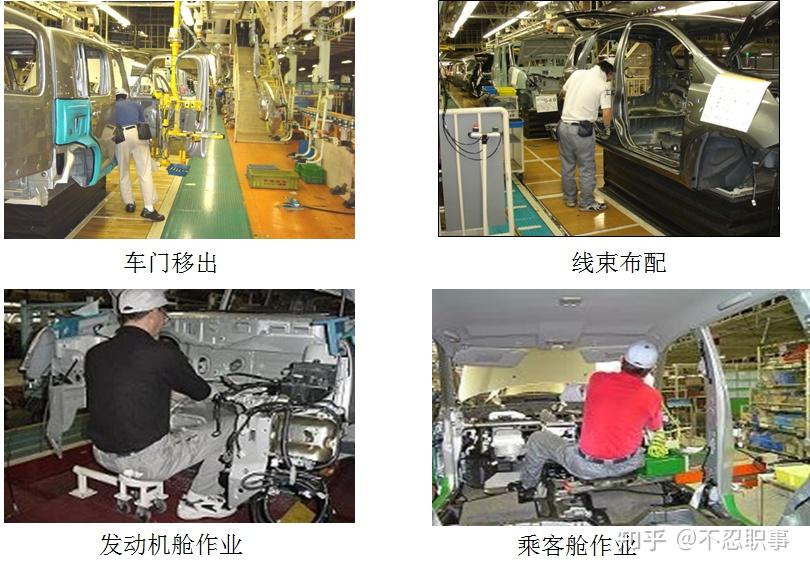
底盘线:一般包含制动管与燃油管,发动机、变速箱与前桥、排气系统组件、减震器以及轮胎的装配。
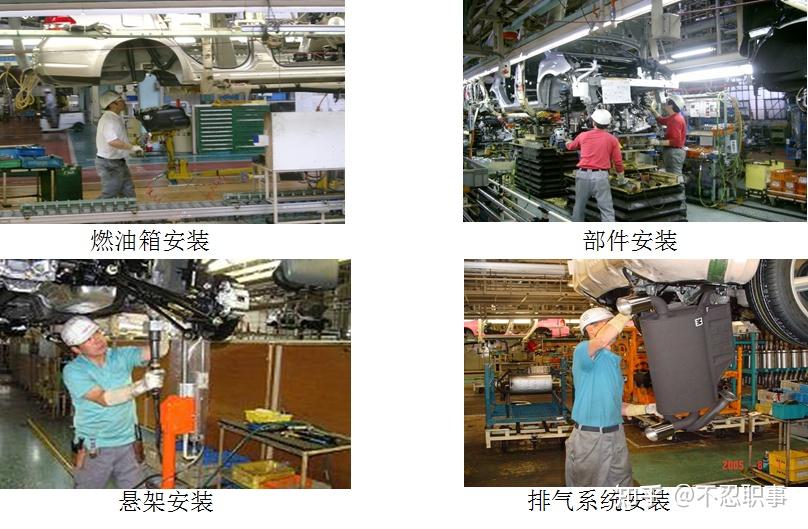
终装线:一般包含座椅和其它小零件、加注制动液、空调冷媒,散热器防冻液以及燃油等。
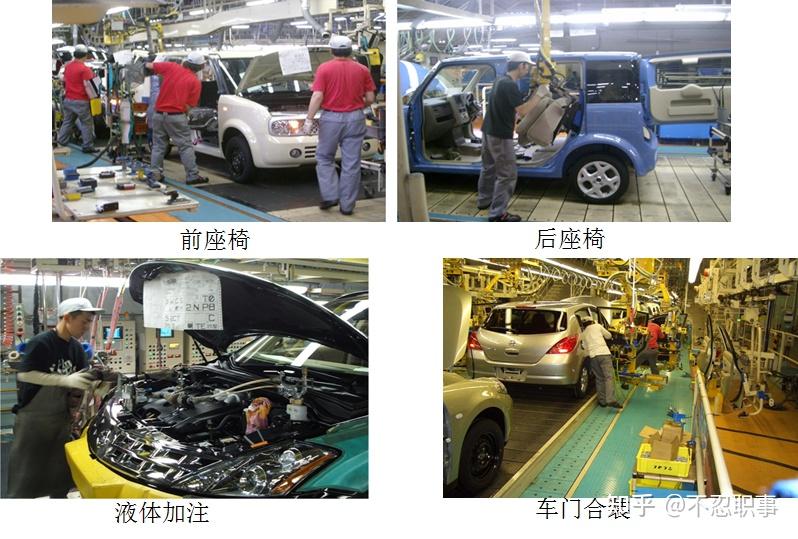
检测线:根据现有安全标准,零部件装配完成后的整车,必须进行全面的整车功能检测。
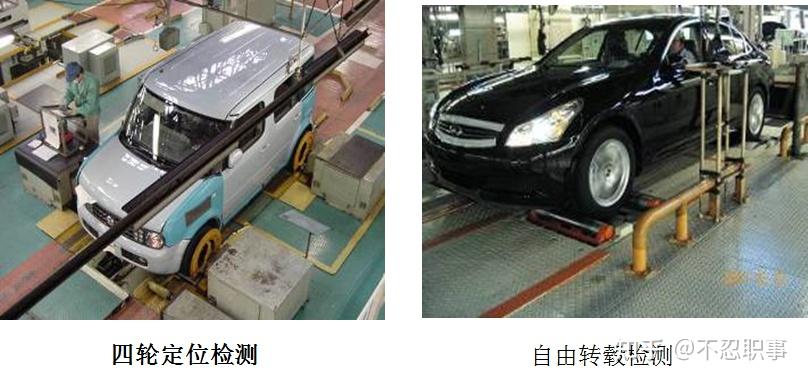
汽车出厂前,必须要经过的环节,对汽车的所有功能是否满足客户及国家法律法规进行充分的检查,确保质量合格的产品交付给客户。
路试检查:对车辆进行动态检测,确定动力系统、刹车系统、专项系统等正常工作,主要包含是否异响、直线跑偏、驻车制动、底盘漏油、及各动态功能的检查。
雨淋检查:在比特大暴雨余量250的冲淋设备里验证车辆是否漏雨,并测试各种灯是否有雾气等测试。
报交检查:对车辆外观及静态功能的检查,确保无划伤、无匹配不良问题交付客户。
谢谢各位能看到这里,要不再看看适合女士的汽车用品
https://www.zhihu.com/answer/2709452828
提这个问题的小伙伴一定是个对世界充满好奇的人。一辆车在制造出来前,需要经历长期研发,从项目策划→概念及方案设计→数字验证(NVH/碰撞/耐久等)→小批量生产实物验证→经历“上刀山下火海”般的各种魔鬼测试→批量生产(Production Trial)→开始进入大批量制造环节,制造过程就像其他伙伴说的,大致涵盖冲压、焊装、涂装、总装四大生产工艺。
现在新能源车已经走入千万家,为大家所熟知。不过市场上有一个广泛的传闻:为什么传统燃油车时代大家很少担心自燃,但到了新能源车,却对自燃忧心忡忡?
必然是因为被新能源汽车各种充电自燃、碰撞自燃等新闻波动着心弦,让人担忧不已。那一辆新能源车在生产制造中是怎样去解决自燃顾虑的呢?今天想结合ARIYA在武汉工厂的生产制造过程,分享一辆新能源车在制造中是怎样确保安全的:
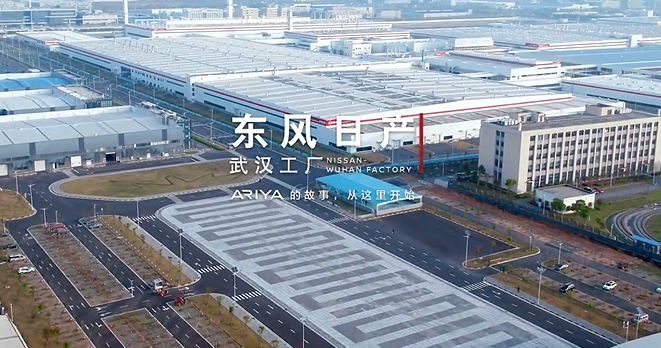
- 面对充电等场景可能的自燃担忧,新能源汽车制造时,尤其要注意电池生产组装一致性管控。
众所周知,新能源车的安全一直是很多消费者心中最大的顾虑,我们会时不时在新闻上看到电动车充电/停放过程中,突然就起火的报道~
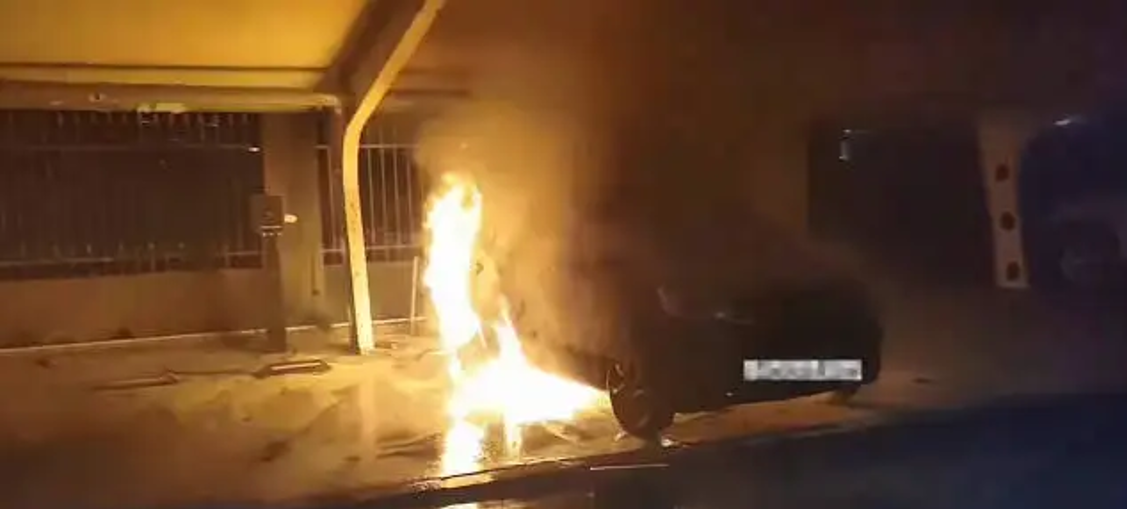
这类自燃很重要原因之一就是热管理系统故障以及电池短路,而电池短路很可能就是因为电池生产过程中不严谨,产生的批次差异,导致电池单体电压、容量、内阻等单体性能存在差异。
那什么算生产一致性不足呢?举个通俗易懂的例子,我们小时候经常会玩四驱车:
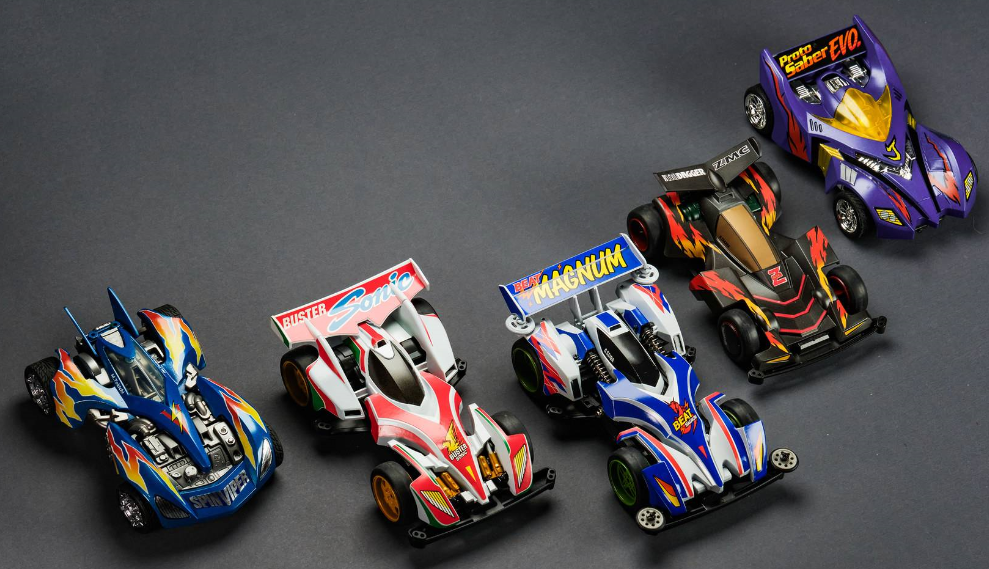
有时候电池数量不够的时候,会用不同品牌混搭,比如一节南孚+一节超霸:
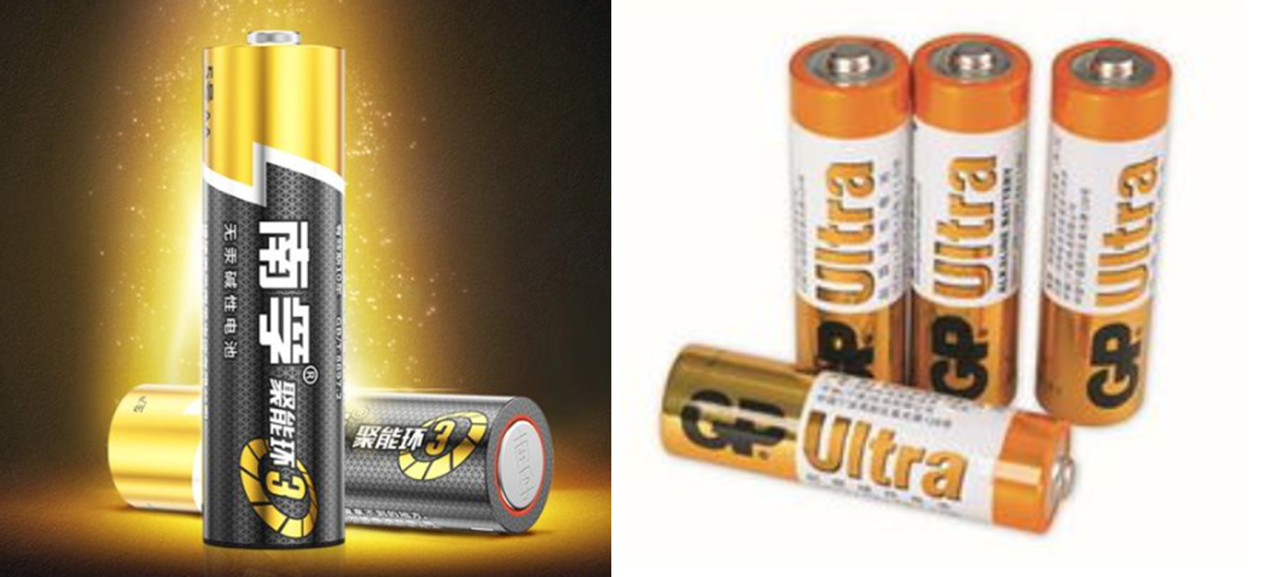
四驱车玩着玩着就会发现,一节电池还有电,而另一节电池没电了。同理,简单来说,新能源汽车电池生产一致性不足就好比在电池包里混装了“南孚”和“超霸”。日常使用过程中会产生部分电池过度充放电,部分电池正常放电,长此以往,就会导致 “一颗老鼠屎,坏了一锅汤”,容易因为局部热失控而导致自燃。
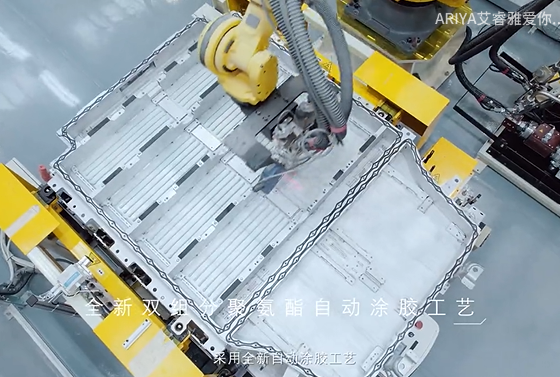
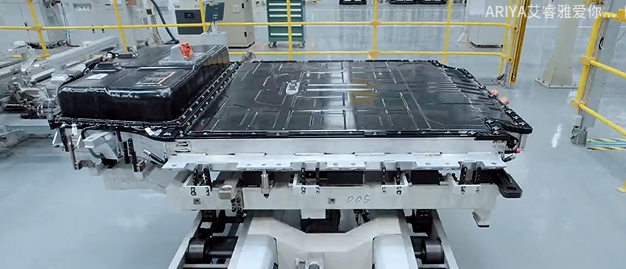
而ARIYA电池包以日产全球标准订制化生产, 过程中100%严格检测筛选,确保电压、内阻、容量、温升等电池内外性能的一致,避免“南孚”和“超霸”混搭产生隐患。
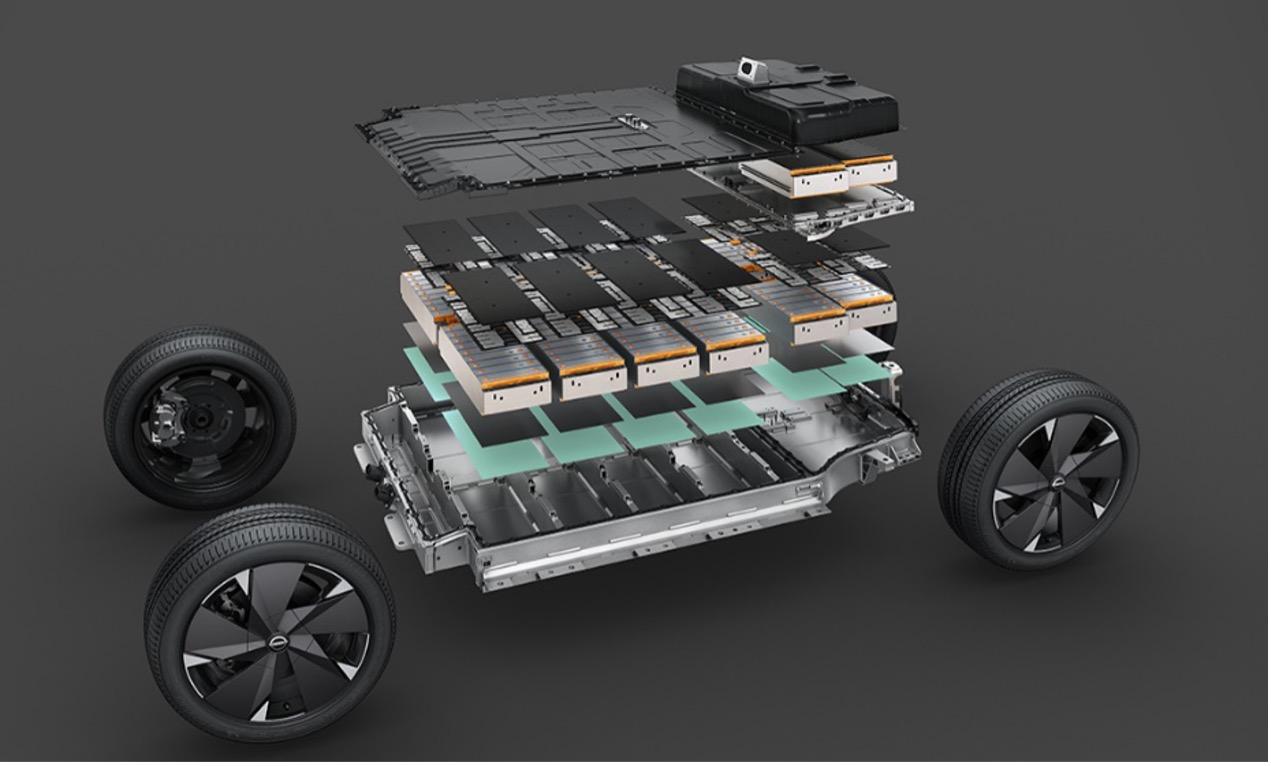
同时采用日产最新电池管理系统,对电池200+项,最短10毫秒进行实时监测,确保高低温环境条件/多次连续快充情况下,电池始终处于最佳状态。
2. 面对碰撞等场景导致的自燃担忧,新能源汽车制造时,尤其要注意做好电池本体的变形防护。
我们时不时会看到电动车行驶过程中碰撞导致起火的视频,这类自燃很重要的原因之一就是碰撞挤压导致电池变形,进而导致电池热失控。
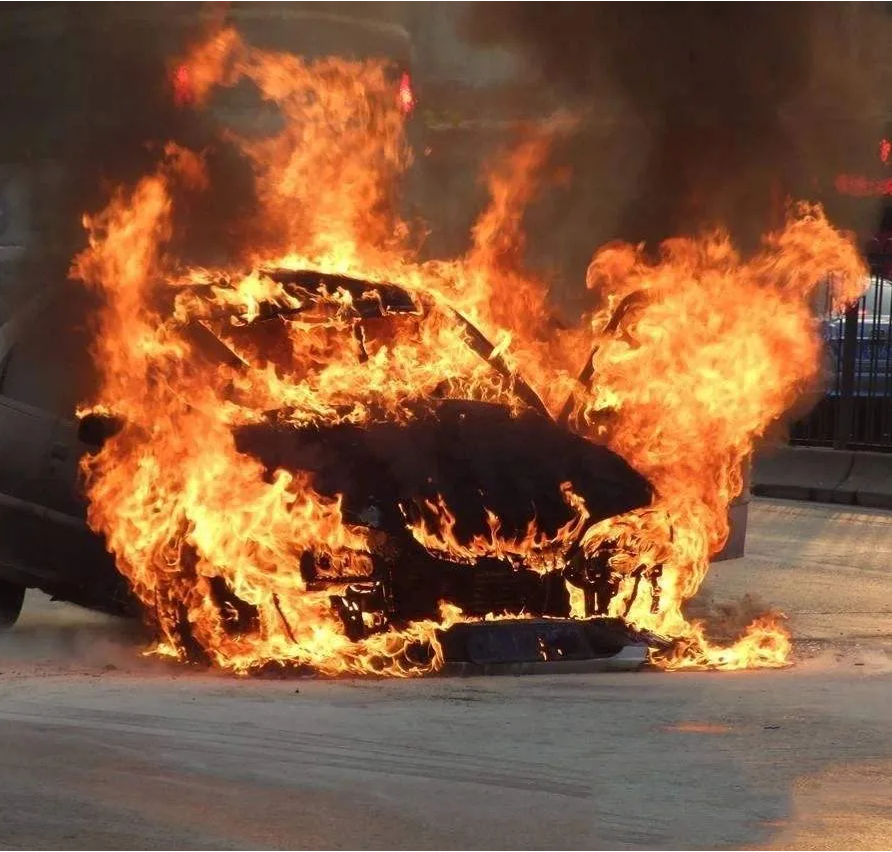
因此在新能源汽车生产制造过程中需要尤其做好对电池的防护,尽可能的防止电池在碰撞过程中挤压产生变形,其中防护措施有很多,比如ARIYA在白车身加工生产过程中,车身关键部位采用1500 MPa 以上的PHS热成型钢,图中红色部分:
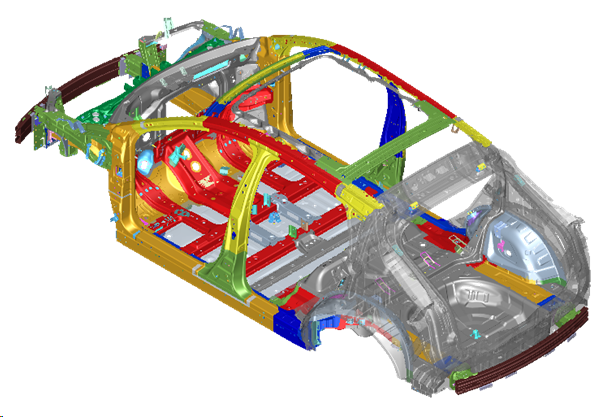
此外,ARIYA全车使用71%的高强度钢(340 MPa以上)和65%的超高强度钢(590 MPa以上),保证碰撞过程中,尽可能的减少电池变形可能性从而降低自燃风险。
生产过程中,超高强钢的冲压制造可有着好大的学问,1500MPa的钢材是怎样的概念呢?做个形象的比喻,就是两只大象(15吨重)穿着一只高跟鞋,踩在了你的小脚指甲盖上。这么“硬”的钢铁想加工成型就需要采用热成型工艺,简单来说就是需要先加热“软化”钢铁,然后再进行冲压成型加工。
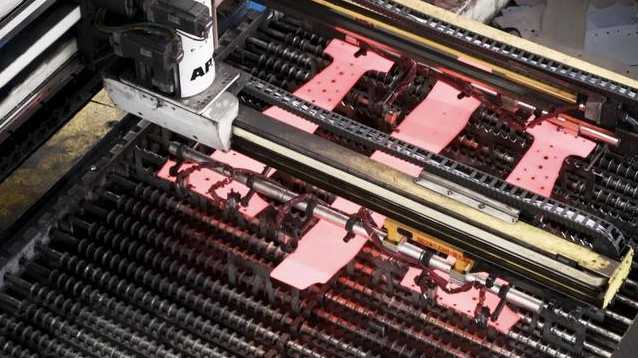
而ARIYA生产过程中采用91%自动化焊装、88%自动化涂装,在冲压(三维光学测量系统)、焊装(超声波焊点检测仪设备)、涂装(全封闭式自动化)、总装(高精度滚床线)四大环节可谓是做到了精益求精。
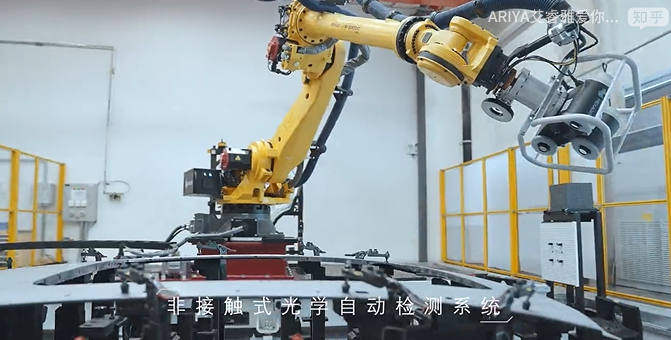
最后话不多说,直接上视频,带你了解ARIYA是怎样制造出来的: